Common Rails Common Problems: Typical Diesel Troubleshooting
Although common rails are an improvement from prior types of fuel systems, they’re not without some issues. Many of these problems, however, stem from things unrelated to the design of a common rail system, which common rail owners should be aware if they want to minimize expensive repairs. Be it common rail Cummins problems, fuel control actuator issues, 6.7 low fuel rail pressure codes, or the like, the following should help you with common rail diesel troubleshooting.
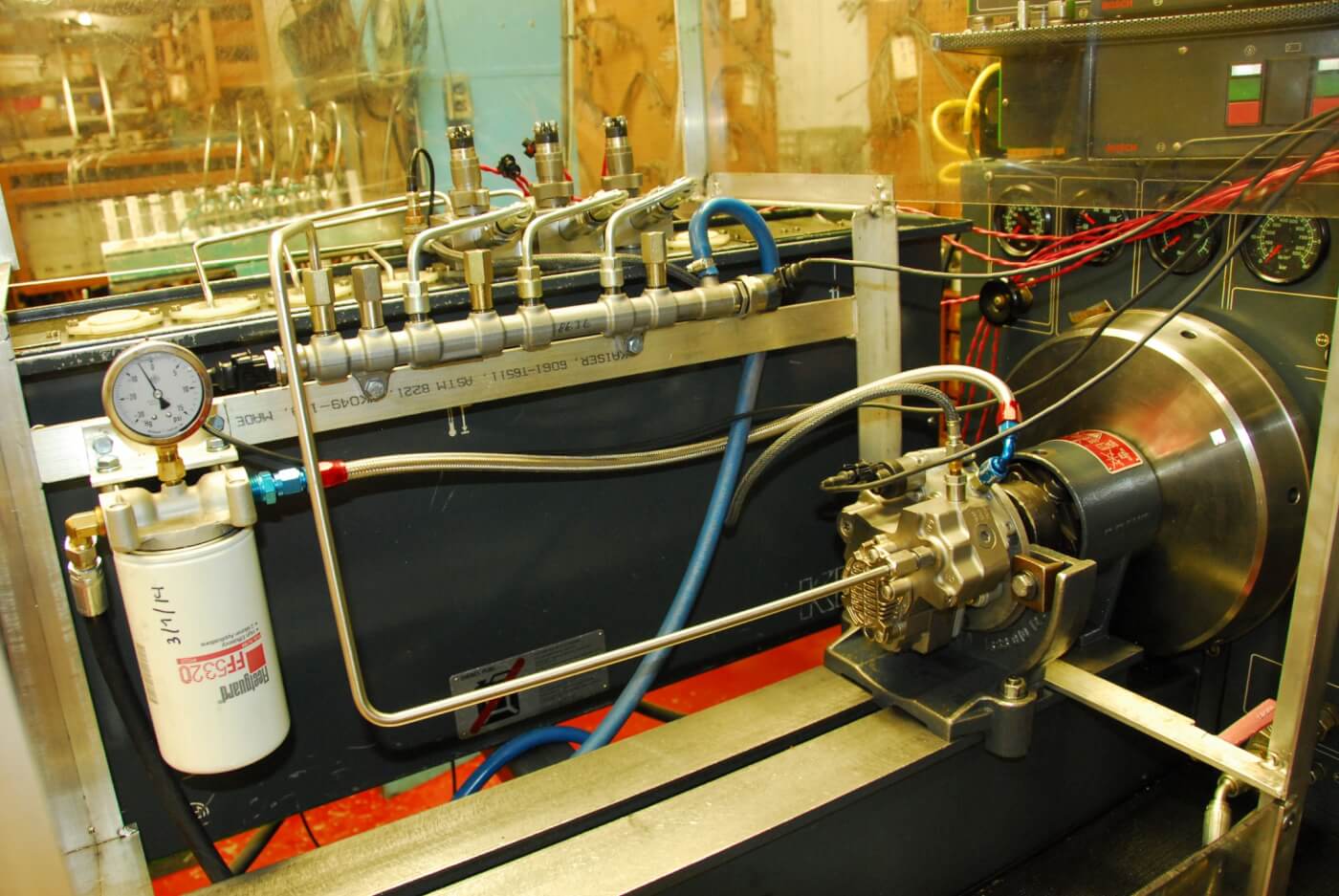
Before getting into those details, we should first clarify how a common rail differs from other types of fuel injection. Then we’ll focus on a few common concerns encountered on common rails.
Note that space doesn’t permit covering every possible fault code on an OBD scanner, or an extensive list of SAE diagnostic procedures, as that would require a massive manual. Instead, we’ll show in the accompanying photos some of the basic steps and tools used to evaluate common rail injectors at an experienced shop, Scheid Diesel. This well-known company not only services a large number of hard-working trucks but also builds championship-winning drag racers and sled pullers. Thus, their technicians know their stuff and are a great resource for repairs and performance upgrades.
OLD VS. NEW
Starting with the basics, a high-pressure common rail fuel injection system (HPCR) used in the GM and Dodge heavy-duty pickups since the early 2000s is quite different from the previously used Pump- Line- Nozzle (PLN) systems (like those found on a P-Pumped Cummins for example, but not like those found on HPOP equipped Power Strokes). Many older diesel injection systems only create about half the fuel pressure modern engines do, and older injectors send the fuel through much larger passages. Also, modern common-rail diesel injectors can fire two or three times per engine cycle, doubling the wear on the injector compared to diesels of the past—hence the need for more conscientious maintenance.
In a PLN system, an inline injection pump handles the following functions: delivery of a pressurized and metered quantity of fuel to the injectors once for each power stroke; control of fuel injection timing; governor control of engine speeds and fuel delivery quantity related to the engine operating conditions.
COMMON RAIL OPERATION
In contrast, with the HPCR system, the engine or power train control module (ECM or PCM) governs the rail pressure, fuel metering, injection timing and engine speed control. Several steps are involved, though, in getting the fuel to the injectors. In a Duramax or Cummins diesel, a low-pressure pump first draws fuel from the tank and pressurizes the fuel to around 10 psi.
Then a PCM-controlled inlet-metering valve (commonly referred to as the fuel control actuator or fuel-rail pressure regulator) controls the amount of supply pressure to the high-pressure pumping elements. This step regulates both the volume and output of the high-pressure (HP) pump.
From the HP pump the fuel flows to the rail where it accumulates prior to flowing to the injectors. Then the injector receives high-pressure fuel from the rail and injects atomized fuel into the combustion chamber as requested by the PCM.
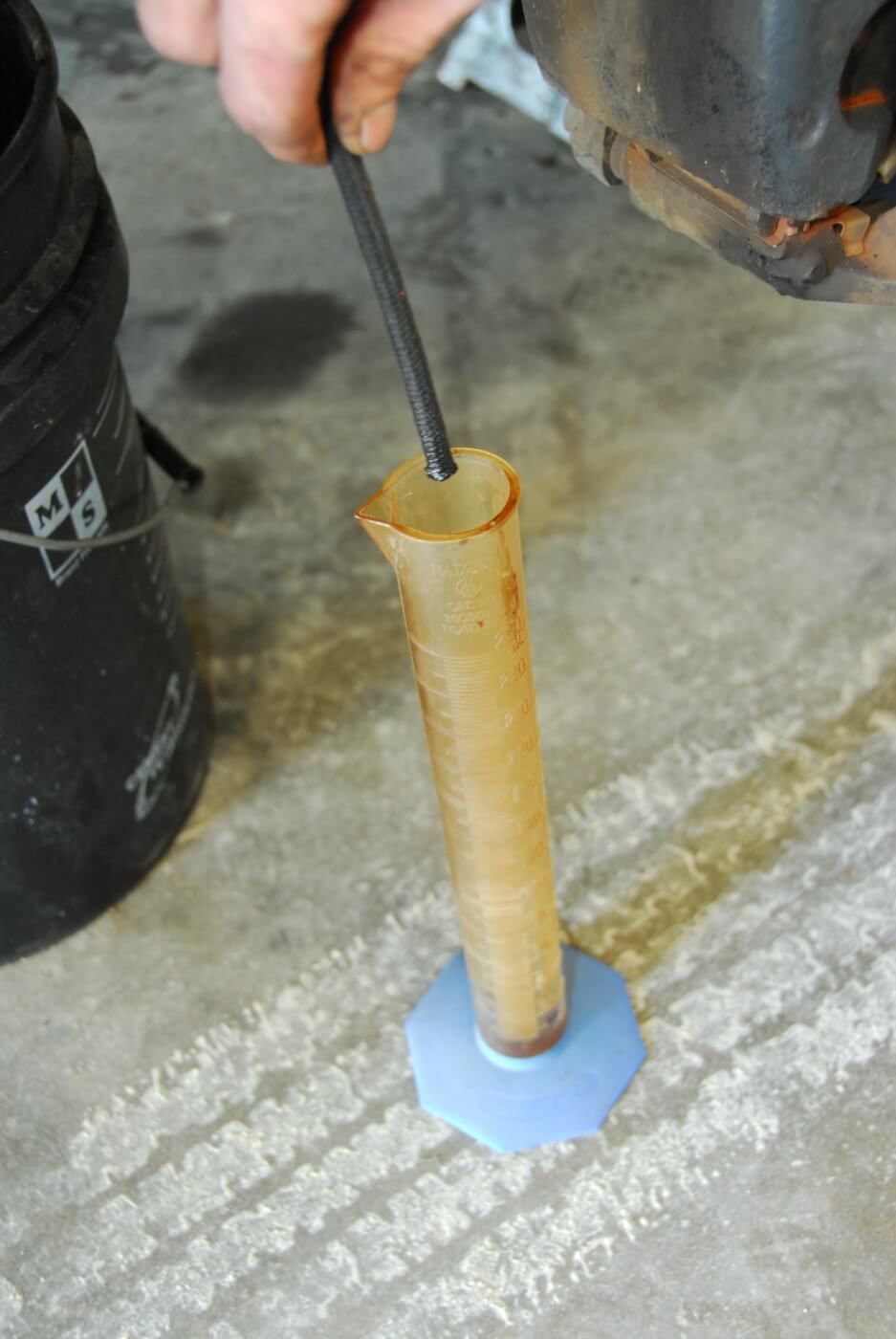
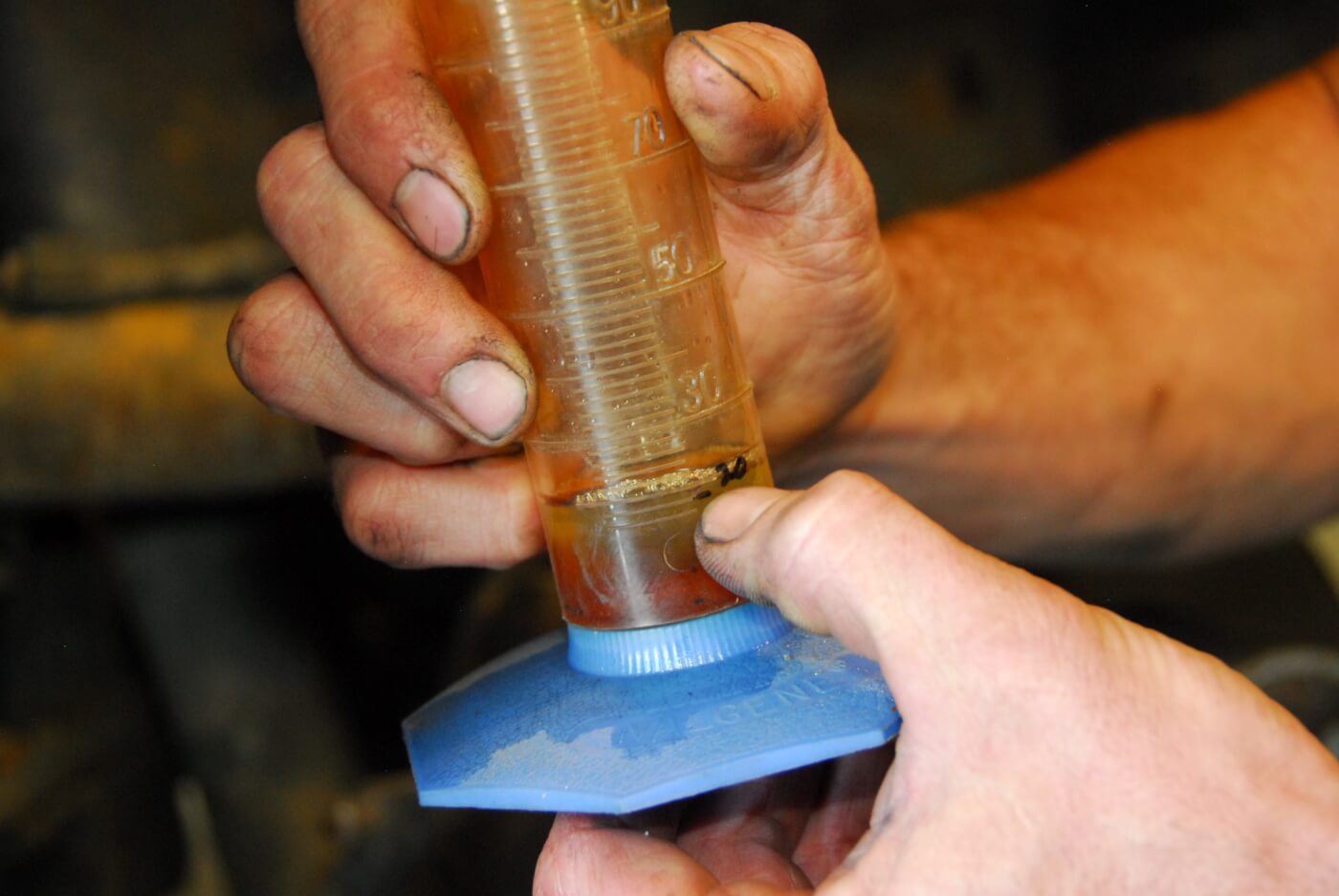
INHERENT PROBLEMS
Given the complexity of the steps involved, several areas can be prone to failure, but often due to a single simple problem: contaminants. As Todd Emmert, machine shop manager for Scheid Diesel, points out, the problem usually boils down to three key words: “Fuel, fuel and fuel.” He’s not kidding here. Aside from debris and particulates, “There’s too much emulsified water in it.”
In other words, that gold tint you might see on fuel components doesn’t glitter. It’s actually a film or residue (what gasoline guys sometimes call “shellac” or “varnish” on a carb) created by corrosion from too much moisture. What this does to an injector is erode the injector’s valve seat in the control valve assembly, degrading the precise flow of fuel. It’s a critical component, since common rail systems have much higher injection pressures, and tolerances are measured out to five-place decimals. This minute thickness makes a human hair look like a tree trunk by comparison.
In the valve assembly, fuel passes through a tiny orifice at very high pressures. The opening is sealed by a check ball only 1mm in diameter. Contamination from water and debris have an abrasive effect on the orifice, grinding the surface, which quickly and inevitably leads to a poor seal between the valve and the check ball. This in turn results in poor injector performance including starting issues, reduced fuel economy and performance, and rough running.
The presence of water also impedes lubricity, resulting in metal-on-metal contact, Emmert observes. Where does the moisture come from? He says that biodiesel is a typical component of most No. 2 diesel (whether it’s labeled as such or not) and it tends to attract water droplets. But moisture can also come from condensation of outside air, leaky storage tanks at a fuel station, or even rainwater puddling on top of an auxiliary tank in the bed of a pickup
Sometimes the HP pump is mistaken as the cause of hot starting, low-power (or no-power) conditions. To avoid any unnecessary repairs, the first thing Scheid’s shop technician Daryn Clapp does is check for diagnostic trouble codes (DTC). The injection balance rate will indicate low compression in a cylinder by displaying the crank-speed values on the downstroke of the piston.
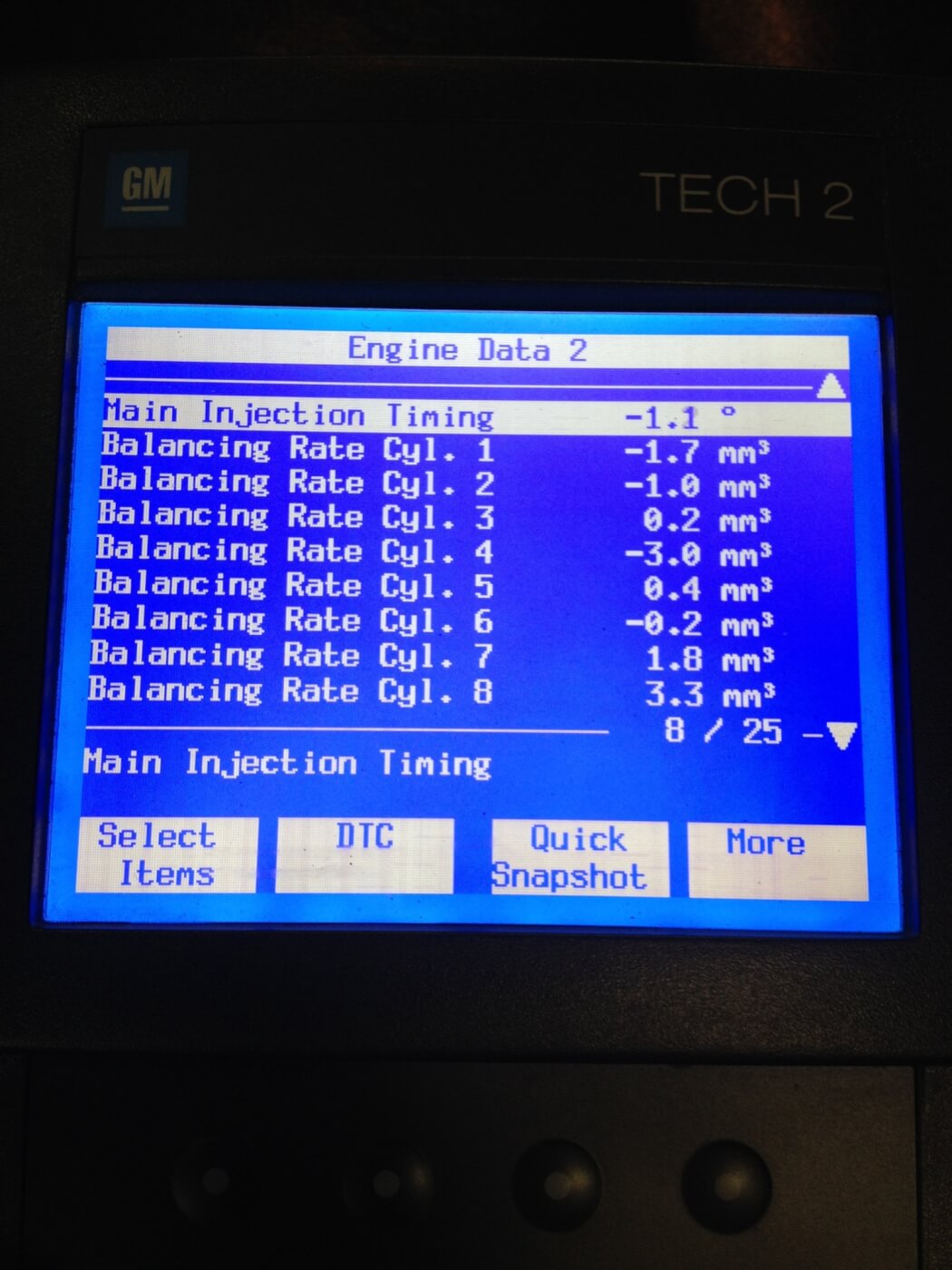
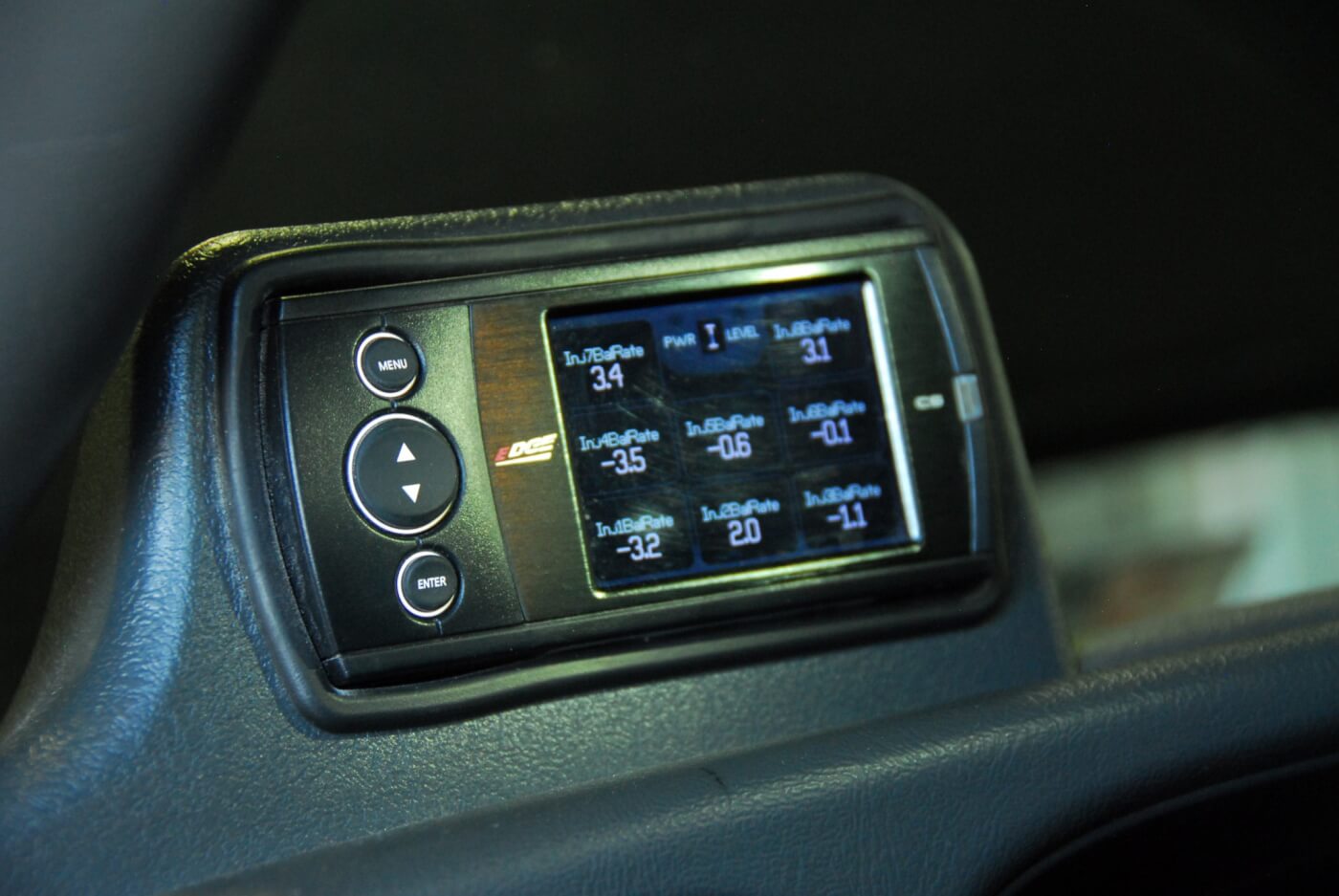
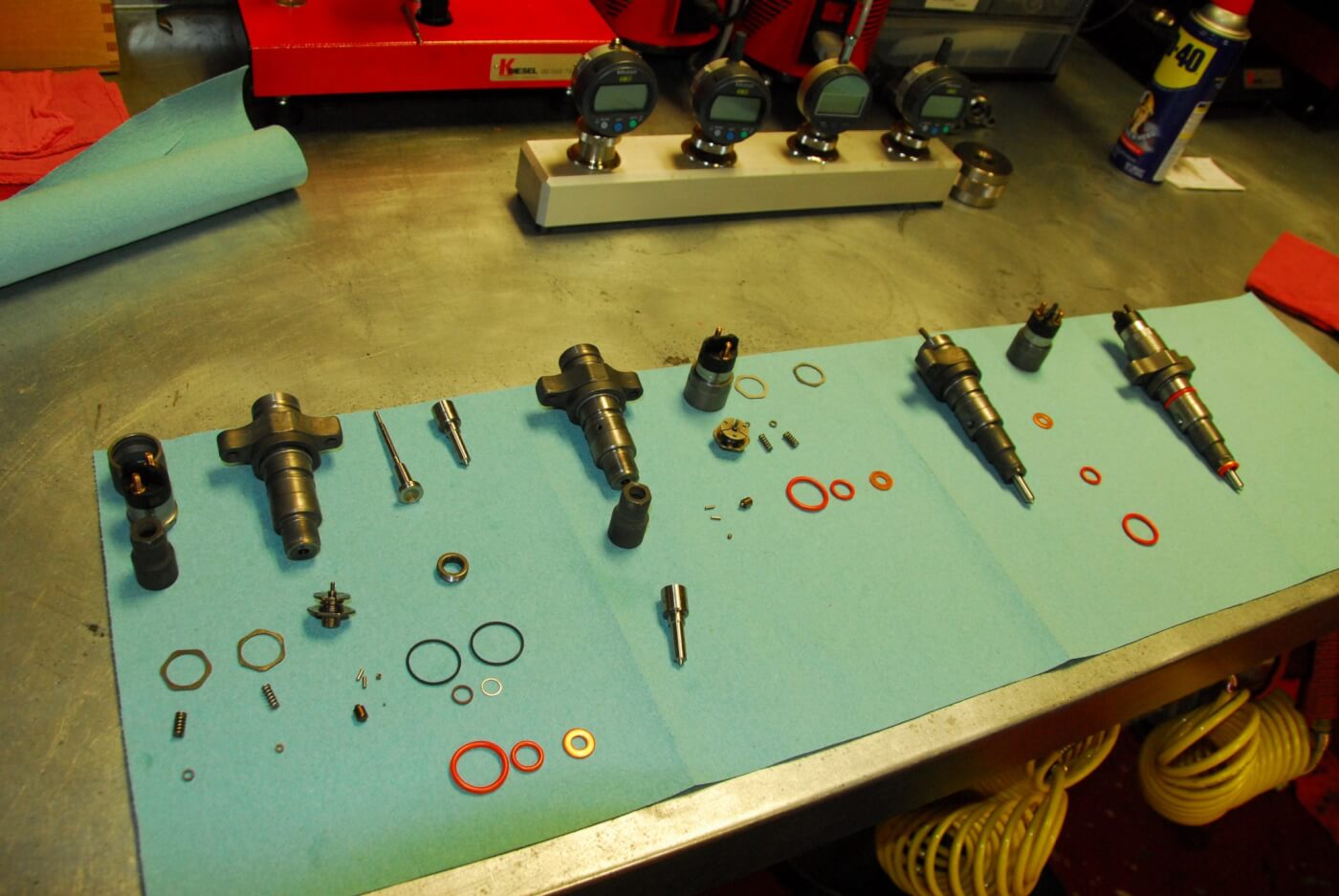
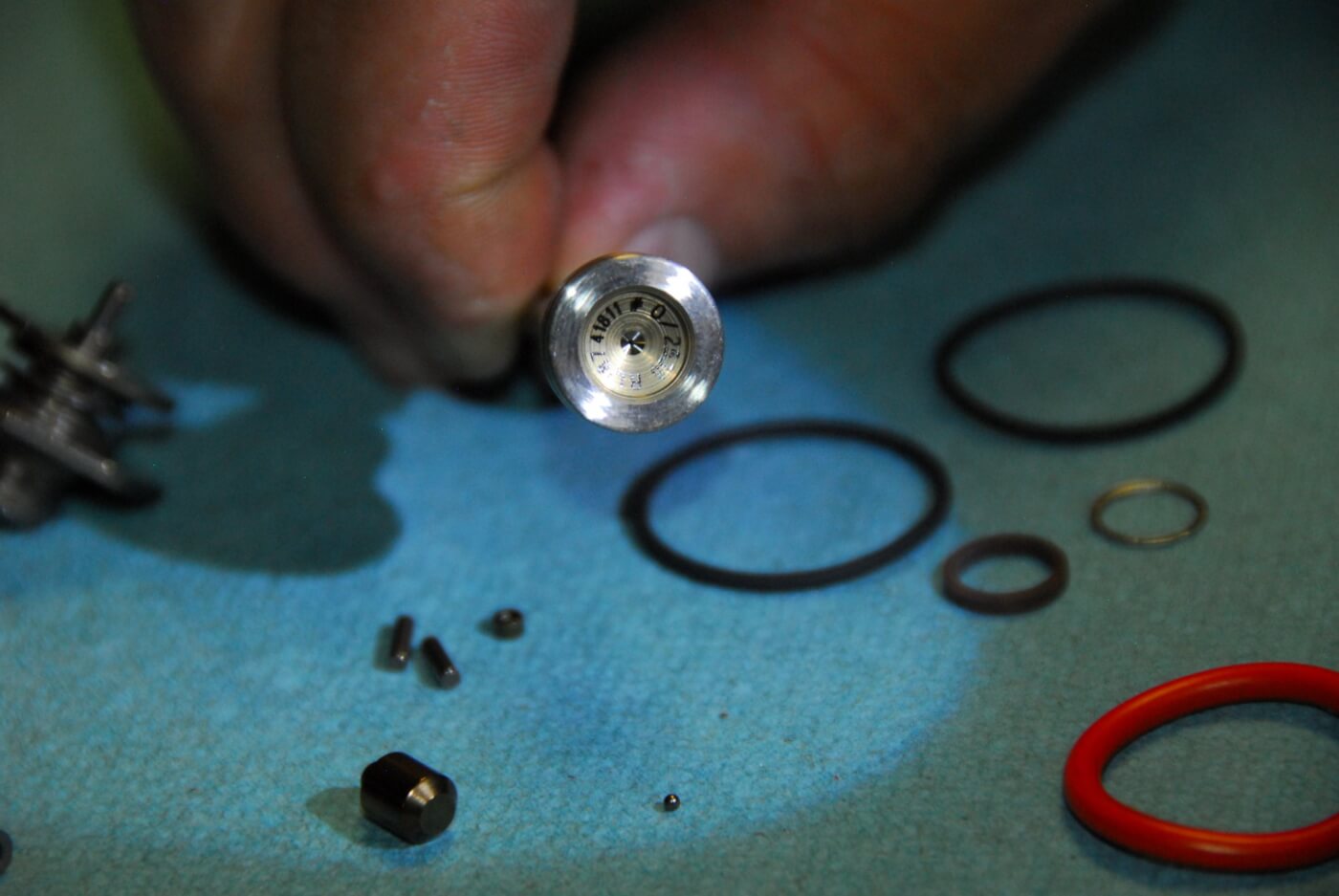
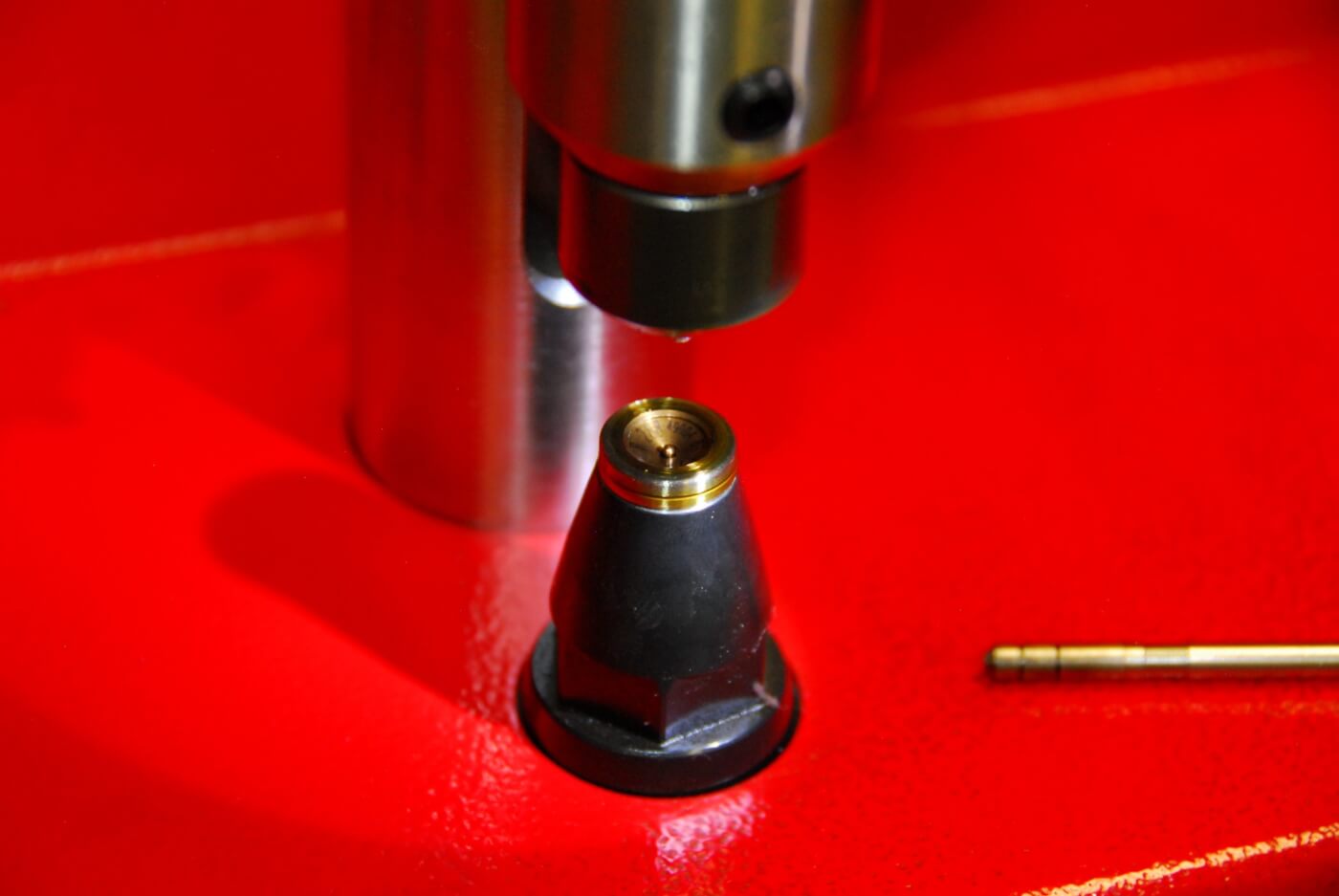
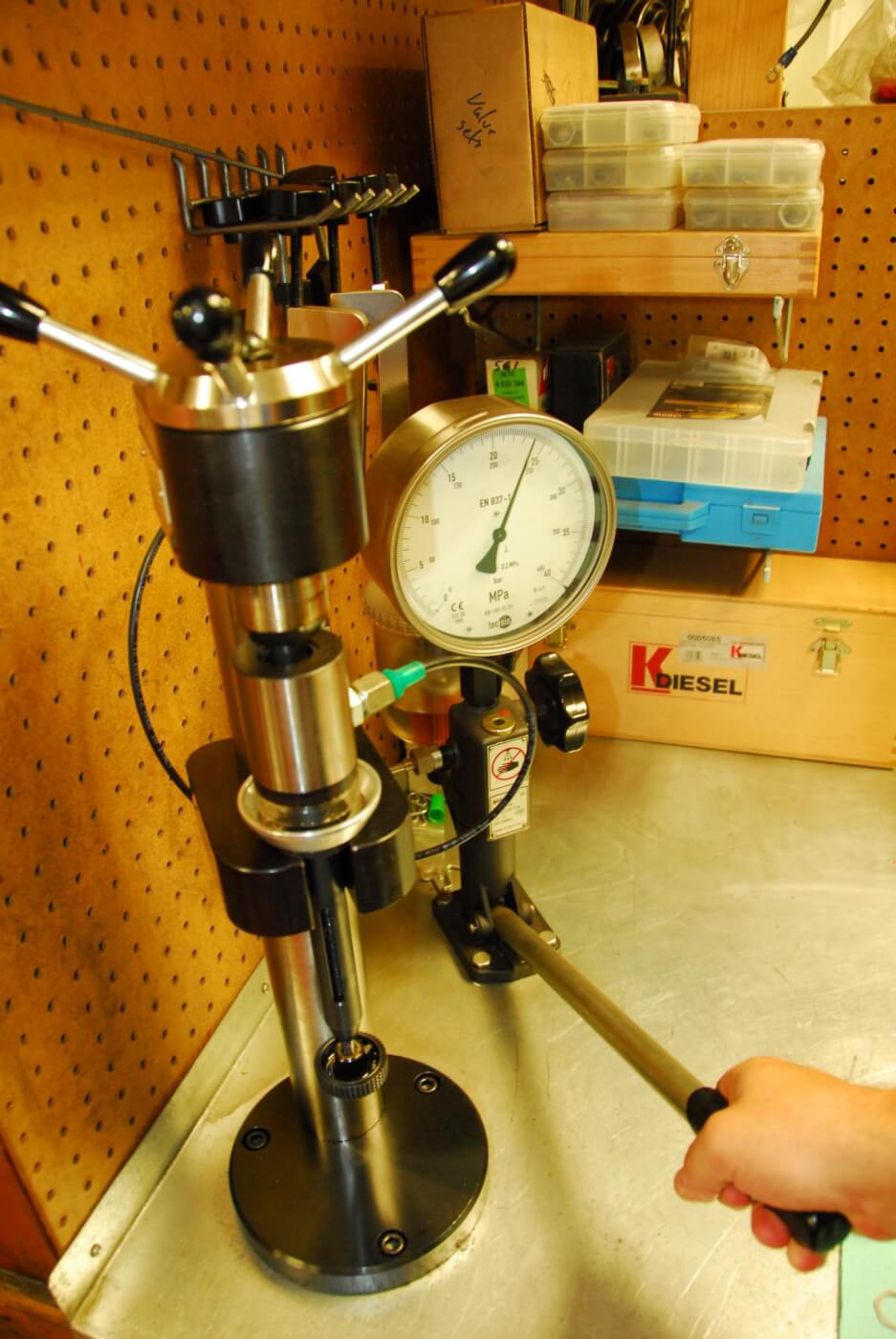
FINDING THE PROBLEM
If the fuel supply system is good, he then might do a quick test of the HP pump. He starts by removing the high-pressure discharge line from the pump, attaching a hose to the line and cranking the engine over until fuel starts flowing out. Then he collects and measures the fuel discharge by cranking the engine for ten seconds three times. If the cranking speed is around 150 rpm, the collected amount should be 70 ml, and at 200 rpm, it should be around 90 ml. If the discharge volume is low, a bad HP pump might be the problem.
The scanner might indicate a short in the solenoid on the injector, by indicating there’s too much resistance in the stator. That can be caused by thermal breakdown on top of the injector, or “just bad luck,” as Clapp puts it. There’s no fix for a broken solenoid—it has to be replaced.
He’ll also check the fuel supply system by measuring the return fuel from the injectors. The method used is fairly simple and gives a clear indication of an injector problem. The return line is disconnected and fed into a graduated cylinder. If the flow is too high (no more than 20 cc per minute) the likely culprit is a worn high-pressure seal.
In some cases, though, such as on a 5.9L Cummins, the issue might be caused by loose retaining nuts on the HPC (High Pressure Connector; part number 4929864), aka cross-over tube. Another possible issue on a 5.9-liter Cummins in particular is with the seal on the cross-over tube on the injector body can be reused if the sealing area of the tip is not damaged. Reusing a good HPC tube not reduces the cost of the repair, but also may save some troubleshooting time as well.
High return flows or connector tube/injector problems can be pinpointed to a specific cylinder by disconnecting one injector line at a time. Rechecking the return flow rate, rail pressure, or trying to start the engine can identify a leaking connector tube or injector.
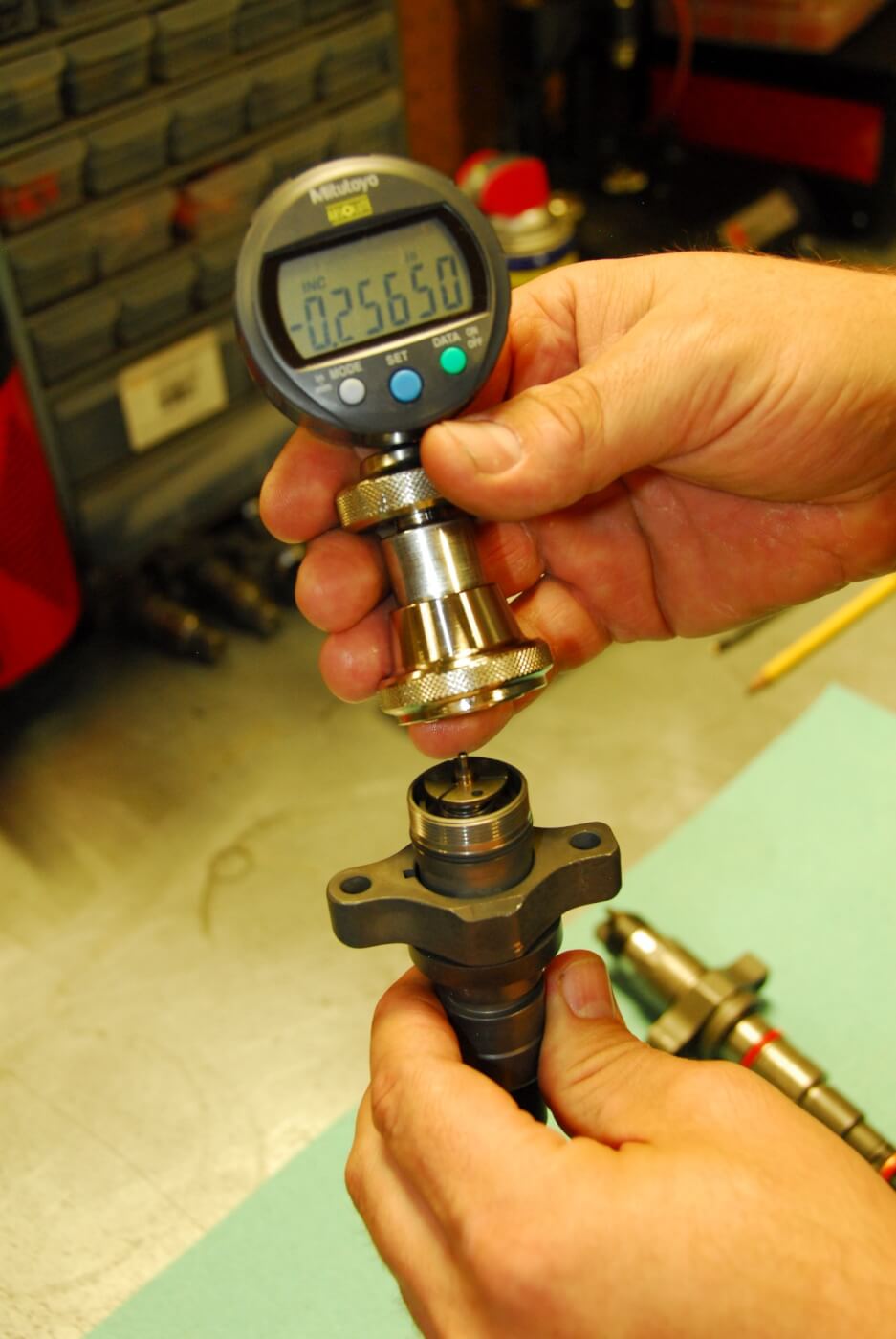
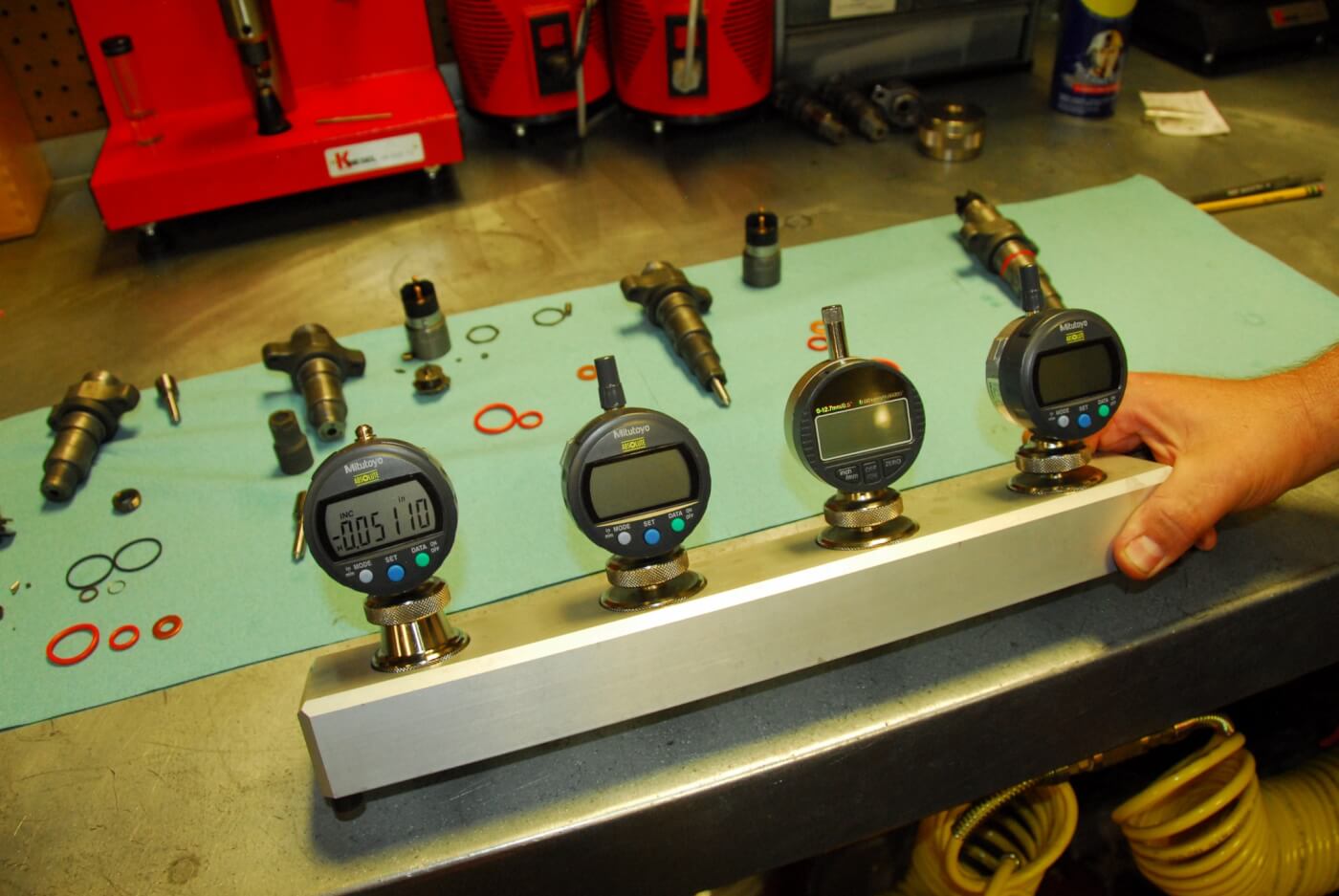
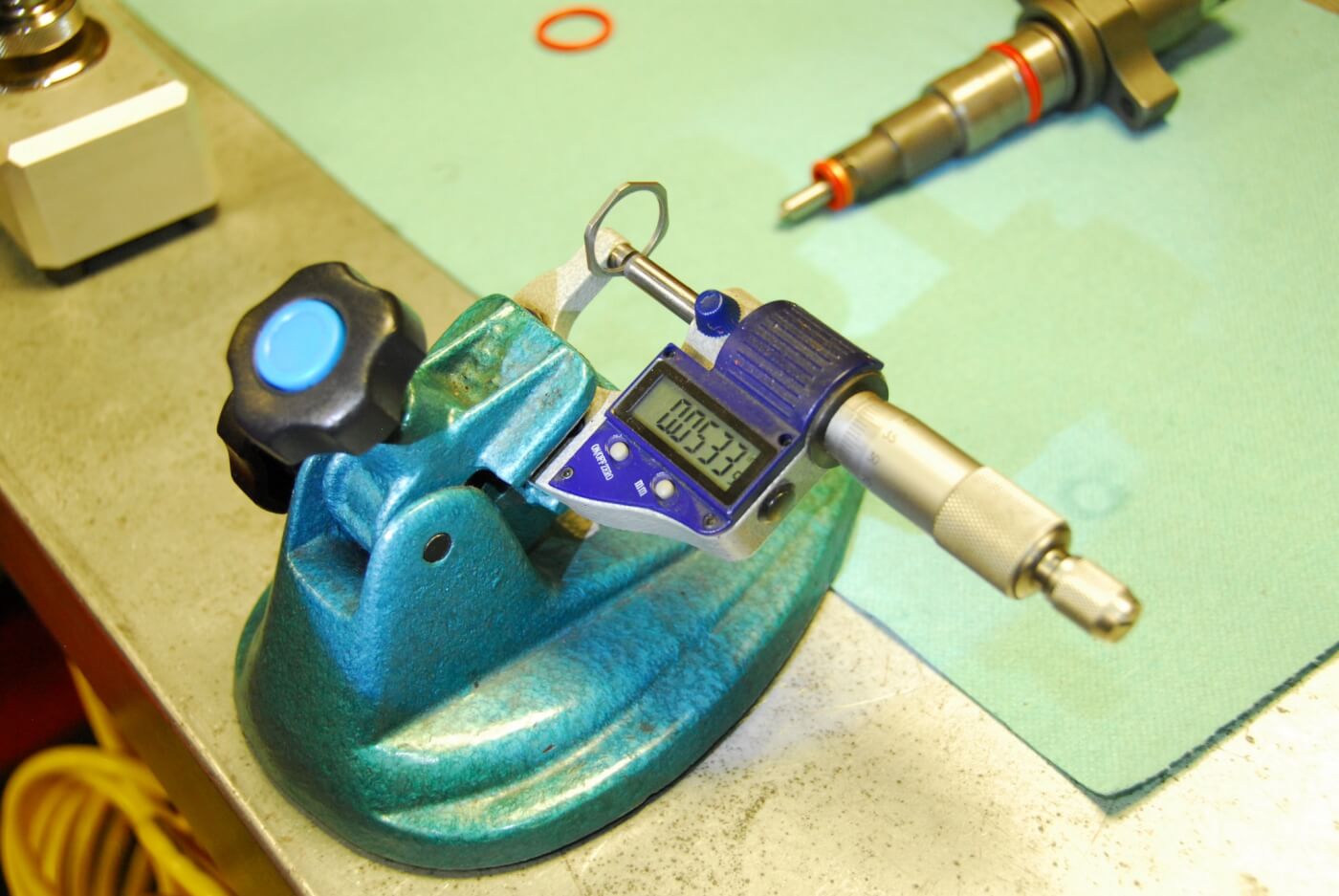
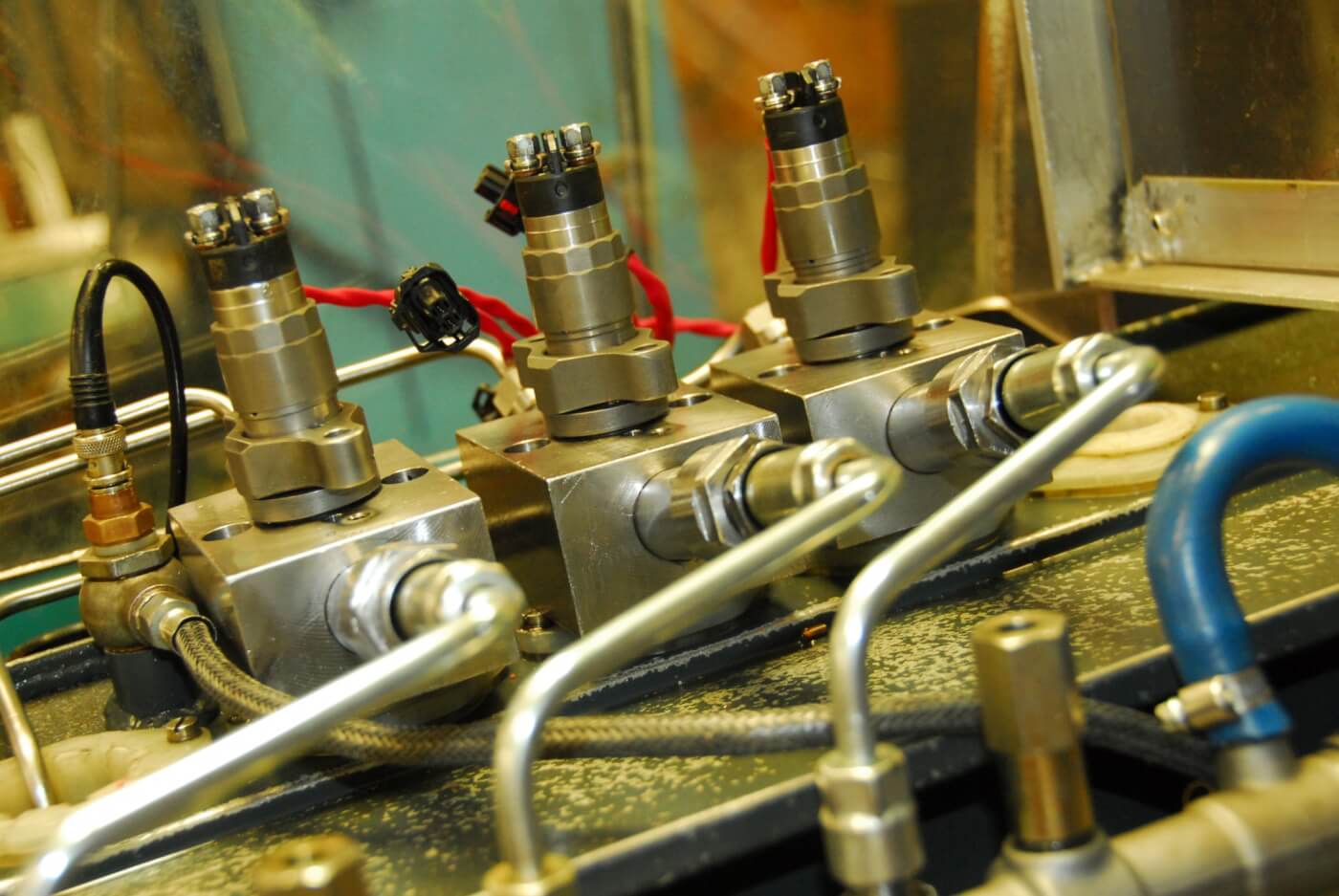
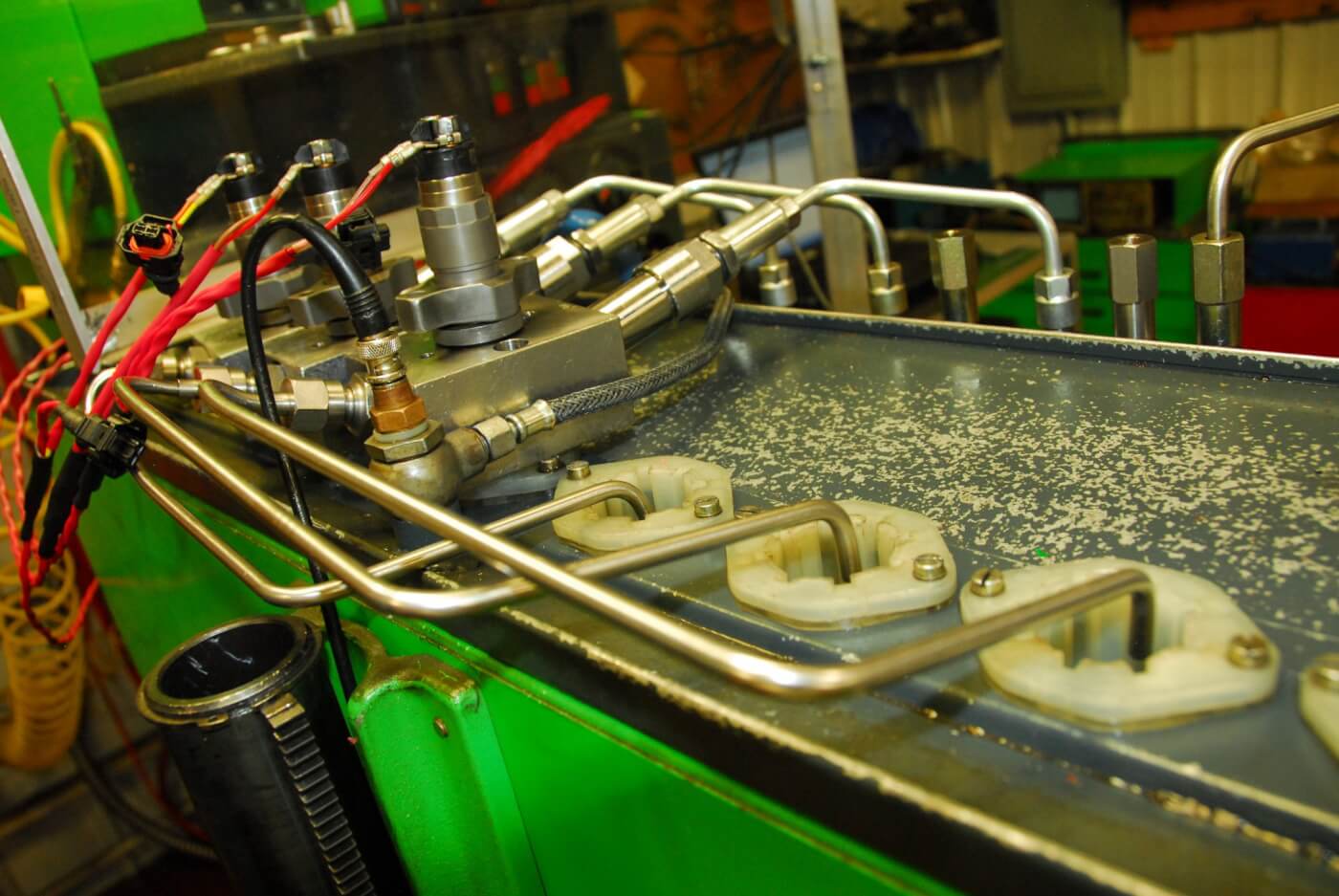
AN OUNCE OF PREVENTION
So overall, what can a diesel enthusiast do to prevent problems on a common rail diesel? Filling up at a well-traveled, name-brand truck stop is a good place to start, Emmert advises. The fuel is likely to be fresher and of better quality.
Check your fuel filters and water-separators often (10,000 to 15,000 miles, or every other oil change). Make sure the water filter screens down to the correct micron level. Also, don’t wait for the “water in fuel” dummy light to come on. Emmert says he’s found a couple teaspoons of water in a separator long before seeing any warning on the dash. And the separator should be checked at a standstill, preferably after the engine has been shut down overnight.
Consider using some water-eliminating fuel additives. Scheid prefers Stanadyne’s performance and lubricity formulas, partly because this company makes pumps and knows how they function and can wear out. He says Scheid is also currently doing long-term testing of Stanadyne’s cleaner for common rails for benefits on DPF maintenance, and the company feels that additive can be of help, as well.
All told, keeping your common rail operating smoothly can be as simple as avoiding that old acronym about computers: “GIGO—garbage in, garbage out.” In other words, a clean (and dry) diesel is a happy diesel. DW
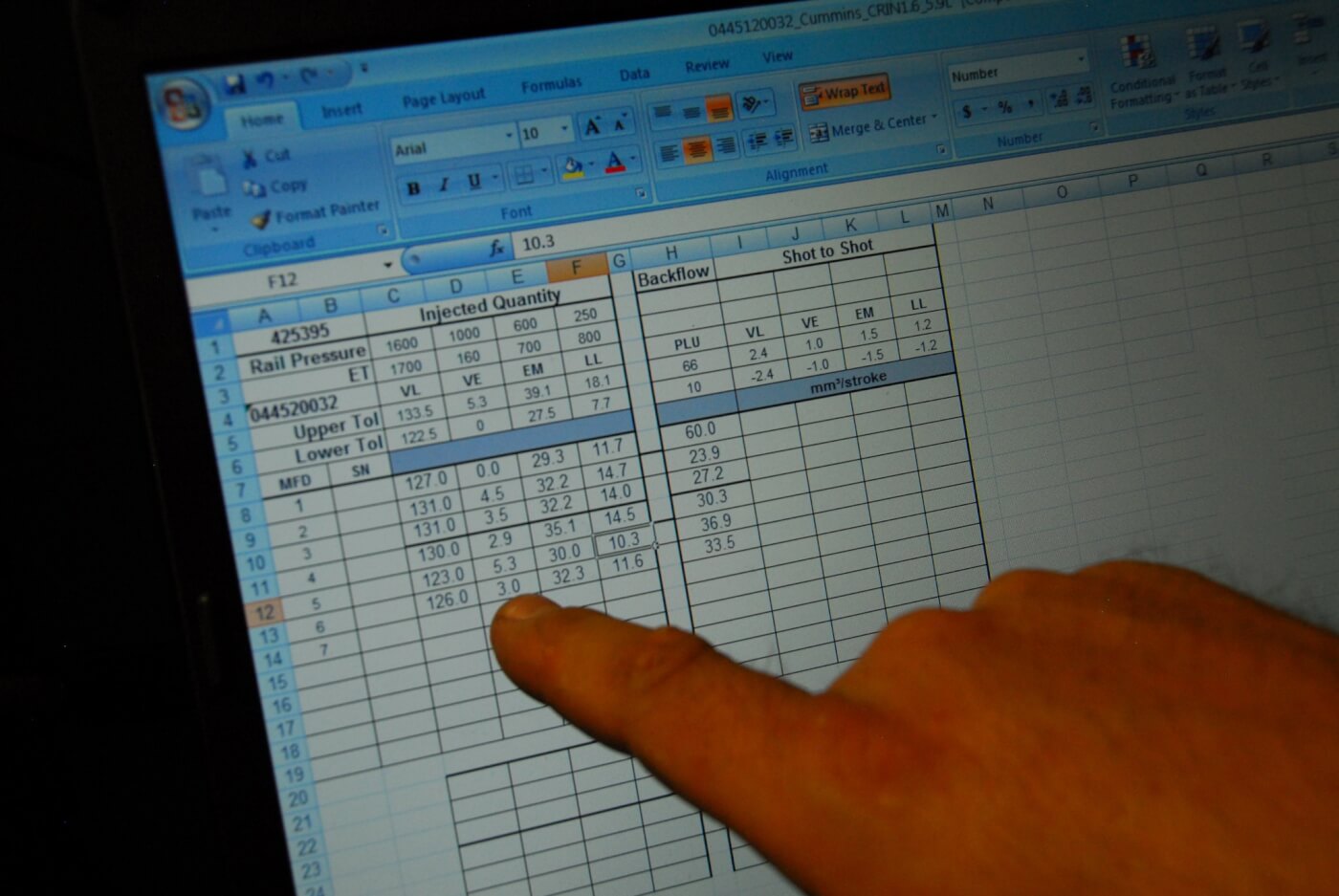
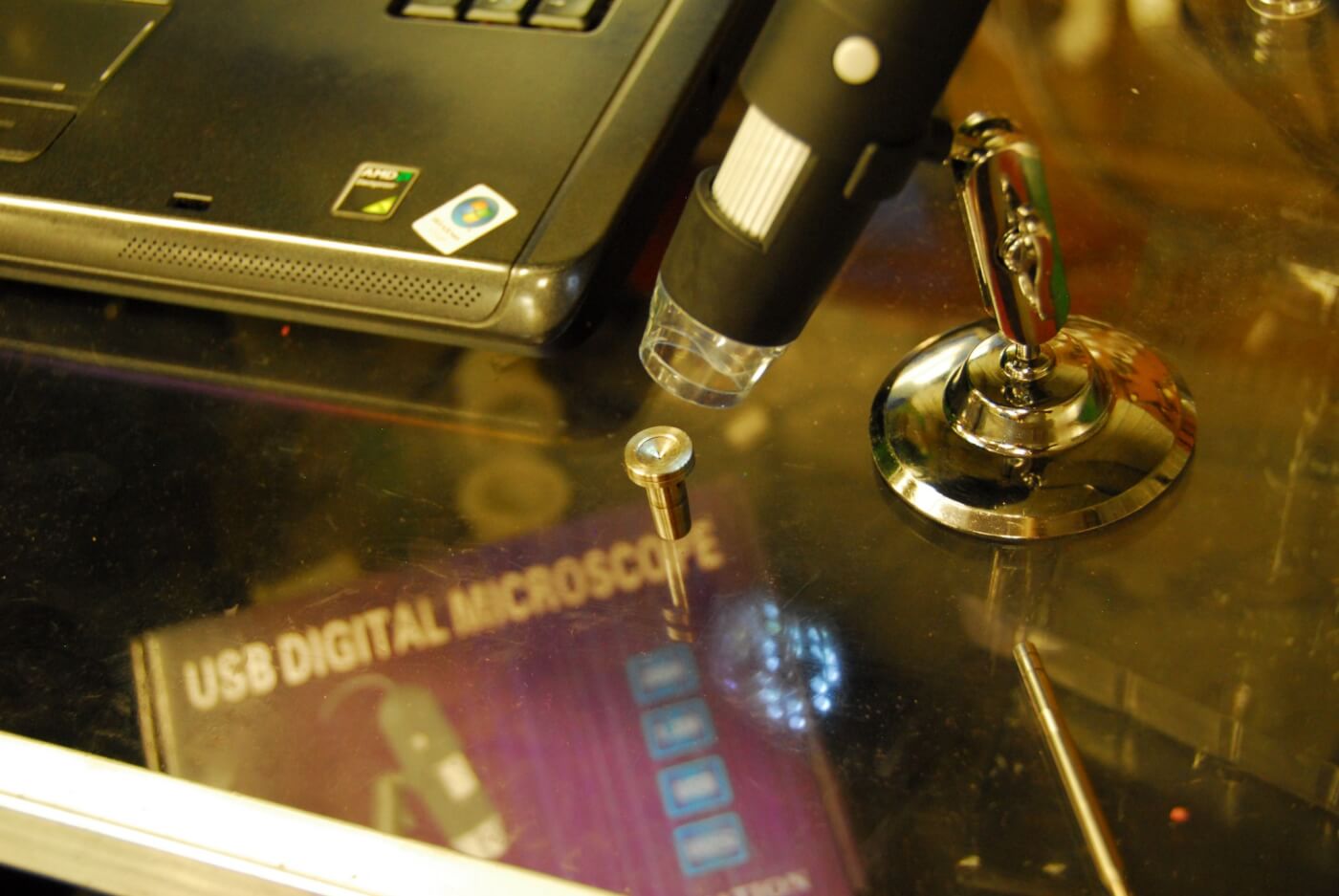
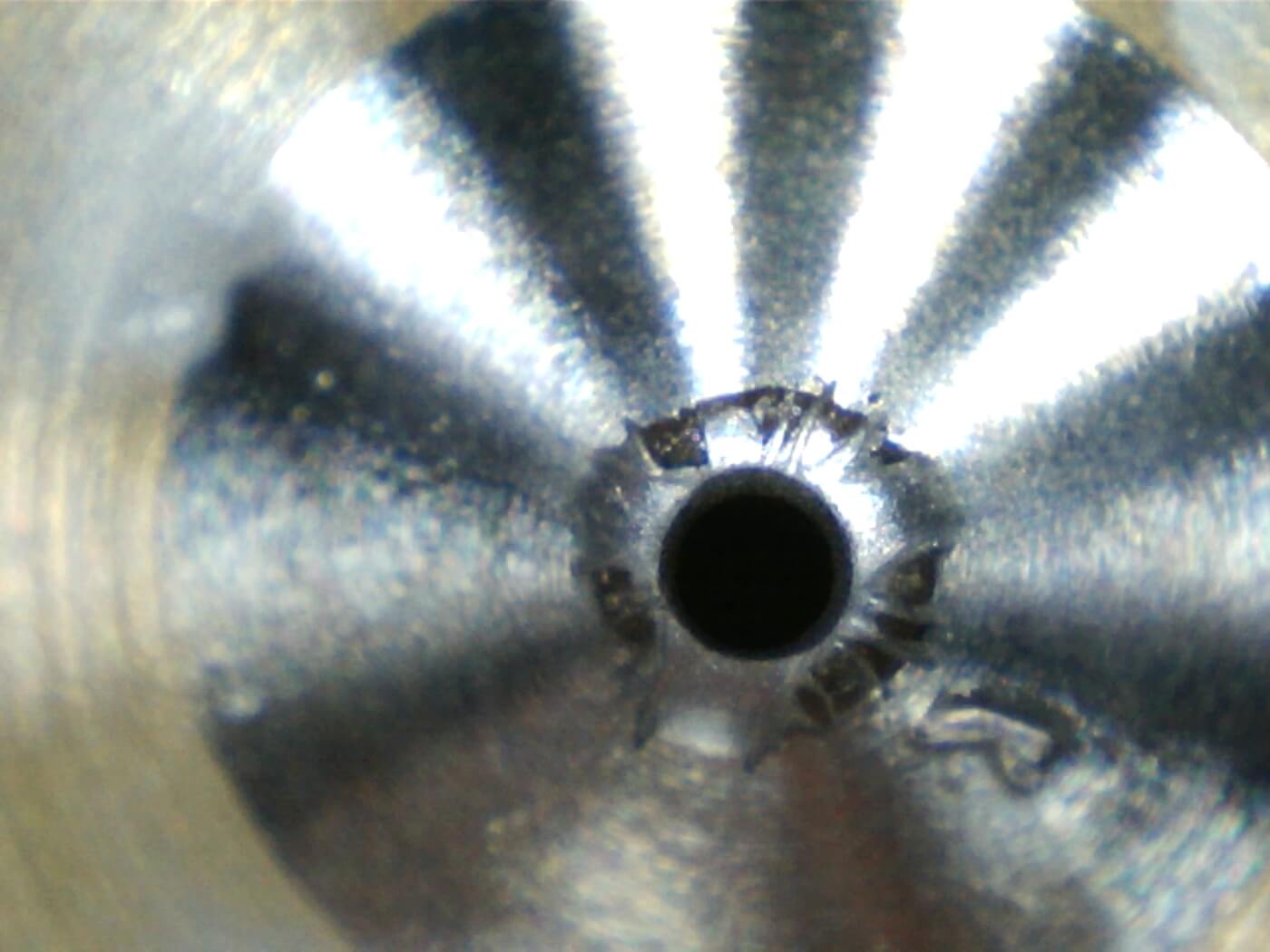
SOURCE:
Scheid Diesel . 800.669.1593 . ScheidDiesel.com