Ultimate Axle Build: Building A Super-Strong 9.25 AAM Front Axle for Your GM or Dodge (Part 2)
The independent front suspension system and 9.25-inch AAM axle delivered in 2001-2010 GM trucks is great at providing a smooth ride on the road, but when pushed hard — such is in dragging, sled-pulling, or running off-road — this axle can be less than reliable. Even if you’re not extremely hard on your truck, you may want to look into upgrading the differential for better traction. (Many trucks have open differentials in the front axle. We prefer our 4×4 trucks to power all four wheels, not just three at a time.) Several Dodge Ram trucks also rely on 9.25-inch AAM front axles and the same differential as GM, so Ram owners wanting more traction and strength than the factory differential offers can also benefit from an upgrade.
Last month we covered the build of the massive AAM 11.5-inch rear axle in our high-mileage 2001 Chevrolet Silverado 2500 HD. This month we will bring you the matching buildup on the front axle. Like the work on the rear, the team at RPM Offroad in Bristol, Tennessee, handled the installation. We previously installed a long-travel Pure-Performance suspension (Diesel World, June 2011), upgrading the weak factory steering linkage in the process. But we knew that the open differential, center axle disconnect and factory CV joints could leave us stranded in the desert if we ran into problems.
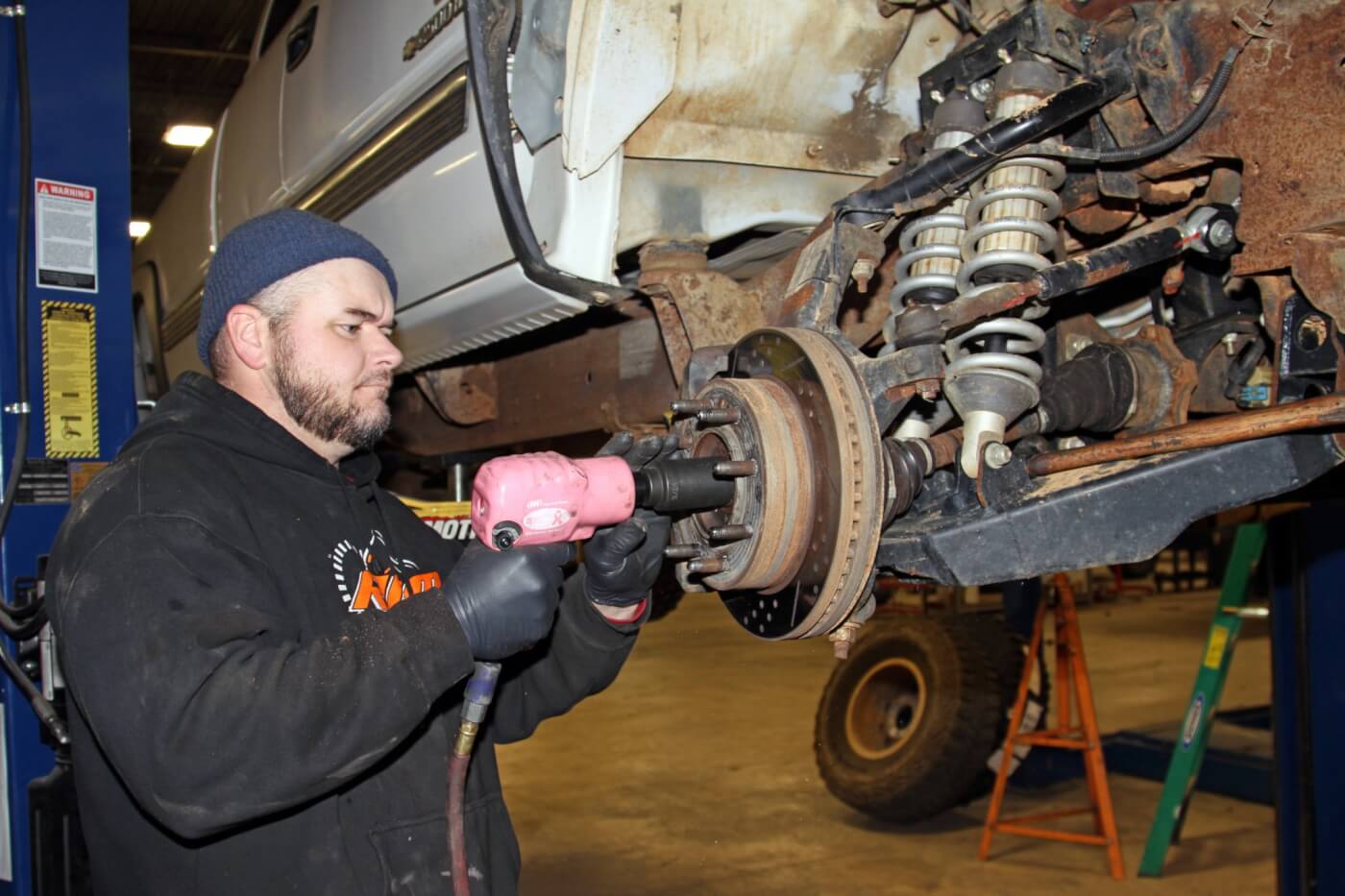
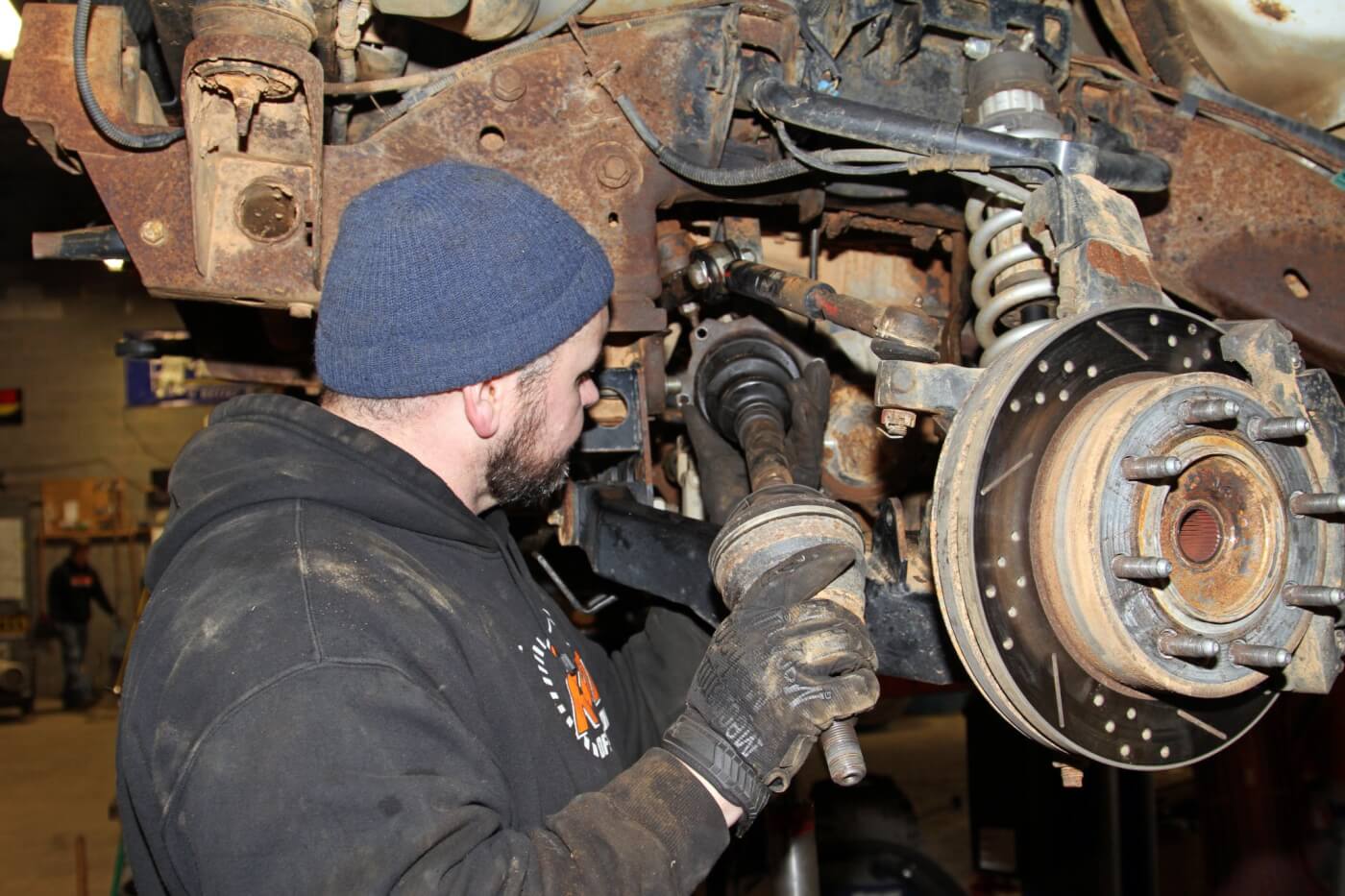
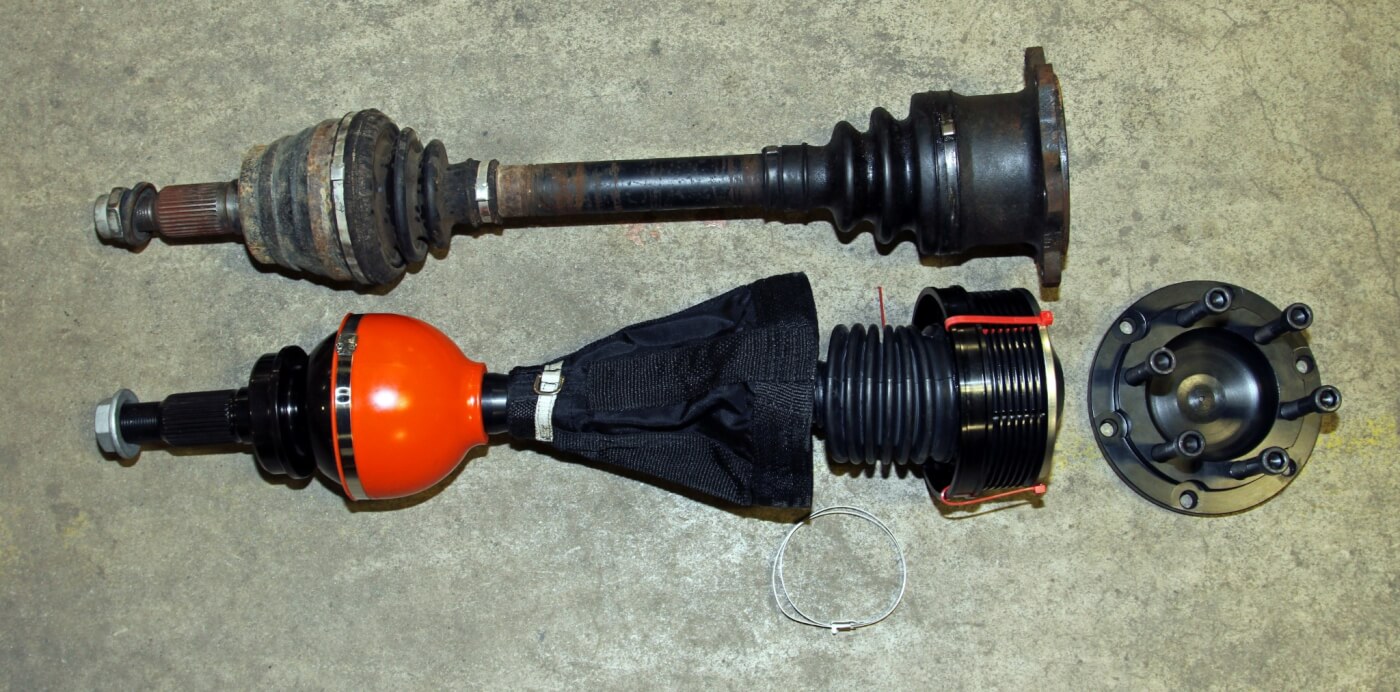
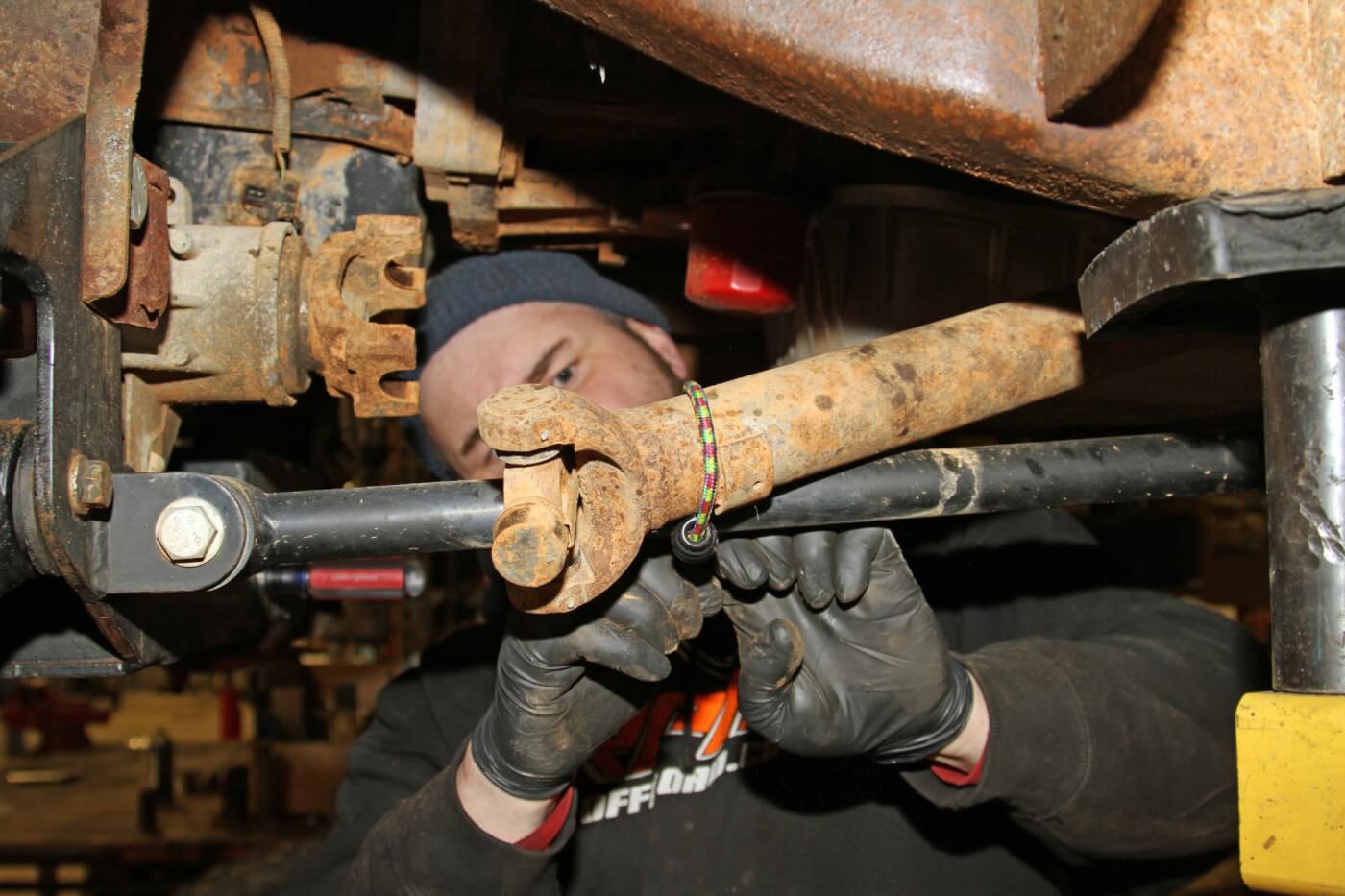
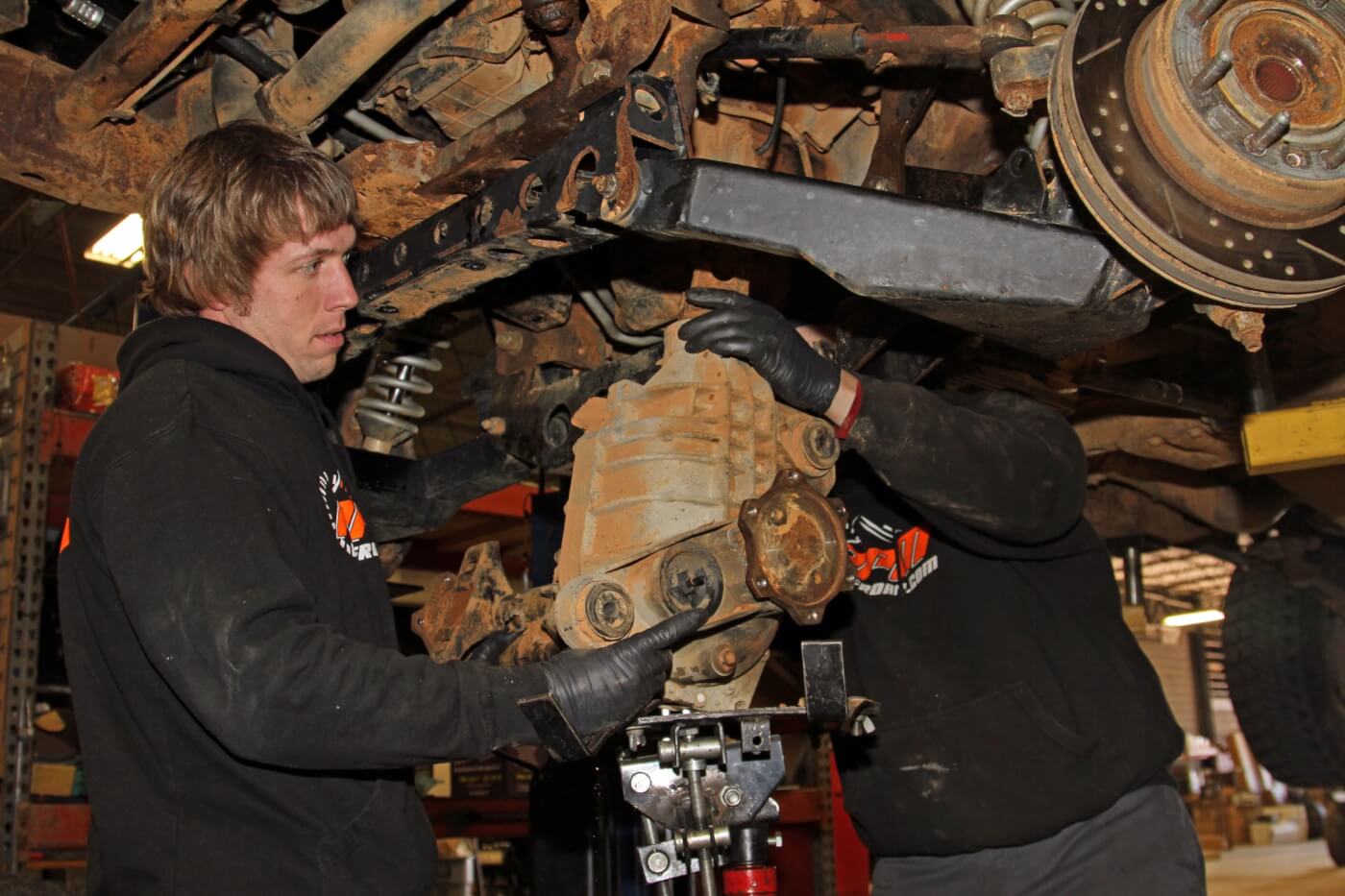
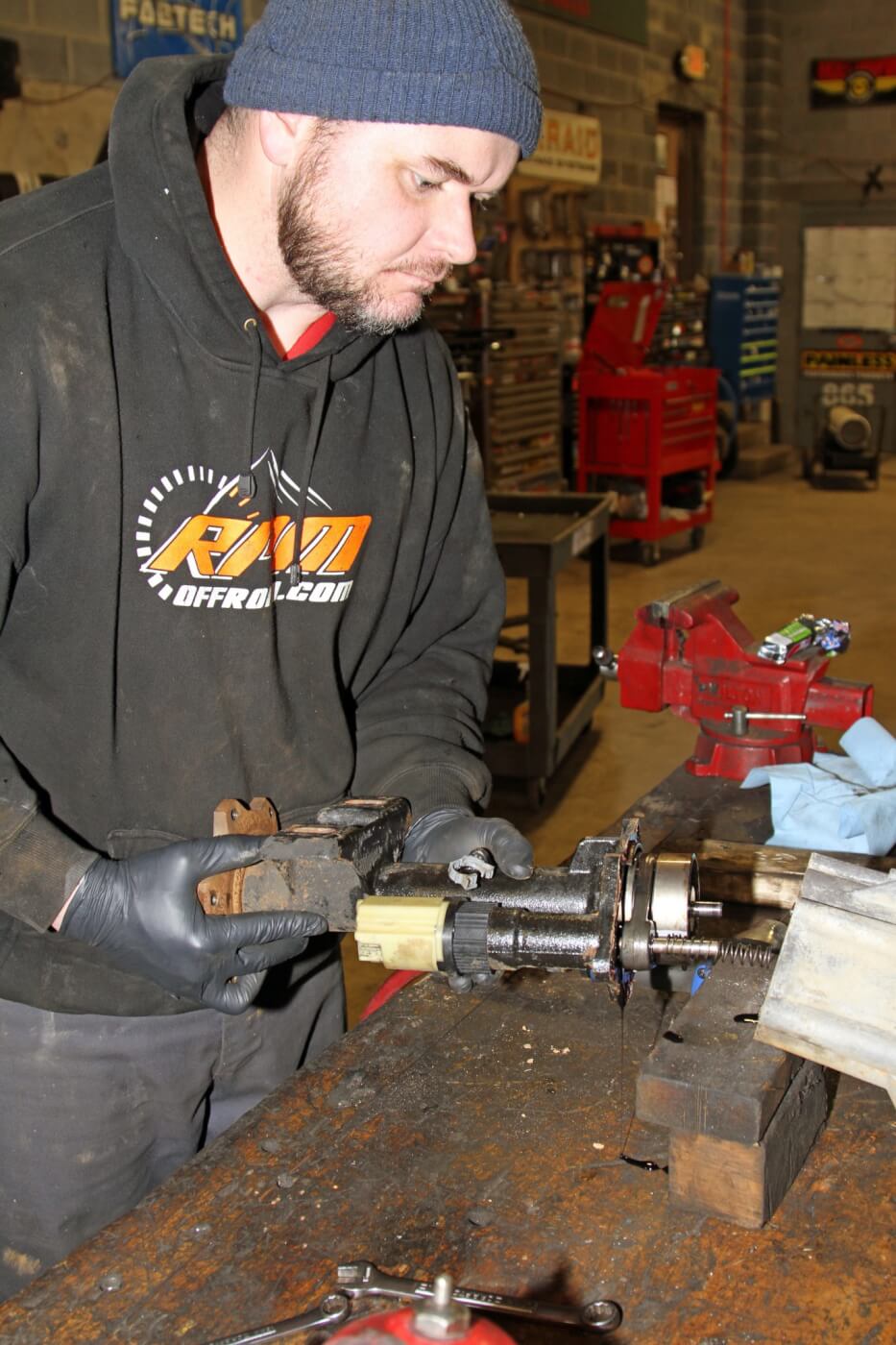
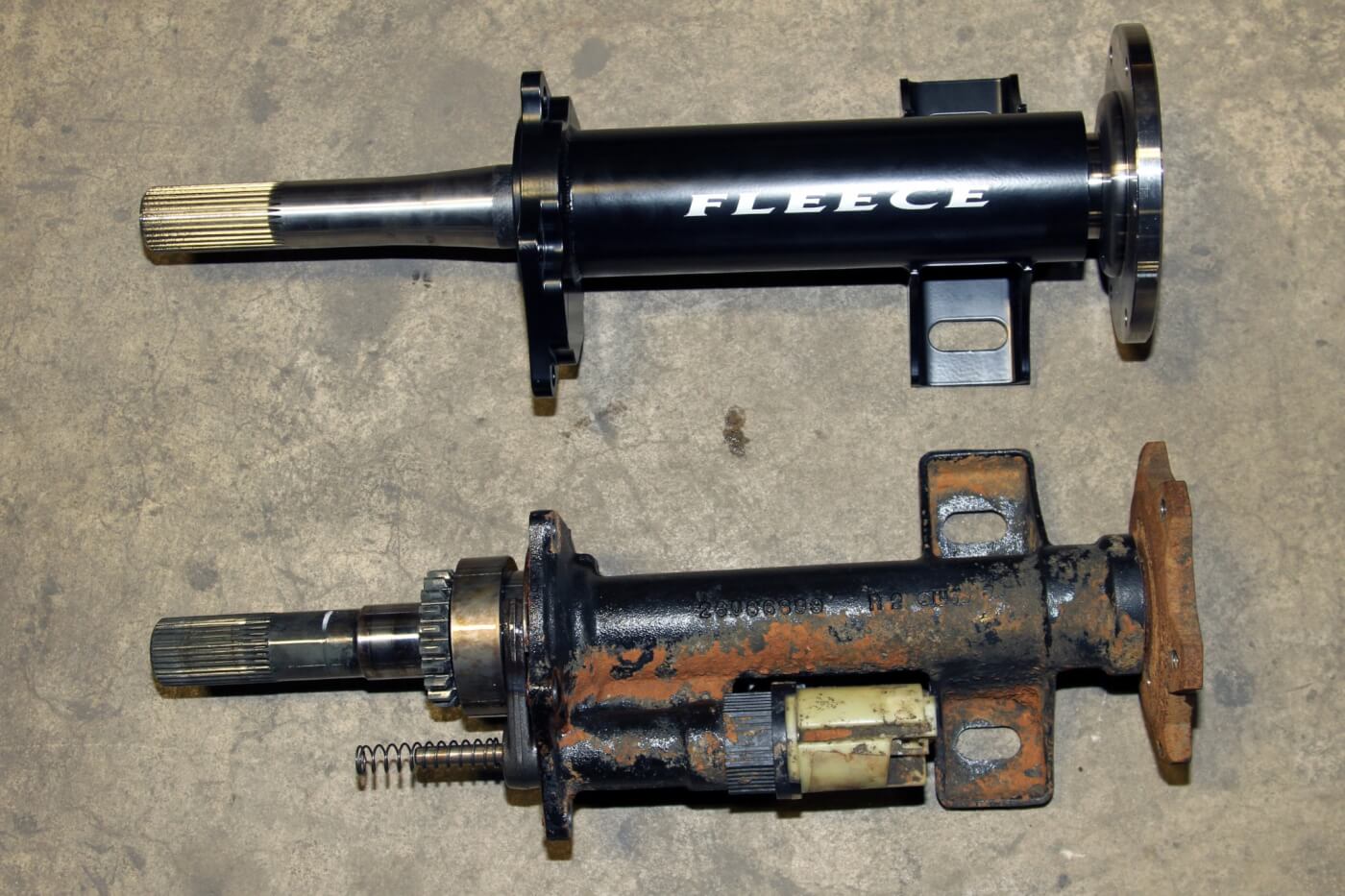
WHAT ARE WE INSTALLING?
As with the rear axle, we will install a set of 4.56 G2 gears with a G2 bearing and installation kit to match the rear and compensate for the large 37-inch Goodyear Wrangler MT/R tires. The gears will spin an ARB Air Locker differential that acts as an open diff under normal operation but locks at the flip of a switch to put equal power to both front wheels.
The factory axle shafts inside the AAM 9.25 housing have been known to break under heavy loads, especially the passenger-side axle with the center axle disconnect. To remedy the axle weakness we contacted Fleece Performance Engineering and ordered a set of their TufShafts, which are made from HyTuf alloy steel. The passenger-side shaft is a one-piece design that deletes the center axle disconnect and eliminates that weak spot.
We upgraded the factory CV axle shafts with a set of custom 300M Branik Motorsports shafts when we rebuilt the suspension, but they were still riding between rebuilt factory CV joints. Since the long travel suspension allows greater CV angles at full compression and extension, we were concerned about the longevity of the factory joints. We contacted RCV Performance and ordered a set of their Ultimate IFS CV Axles built to work with this truck’s increased track width.

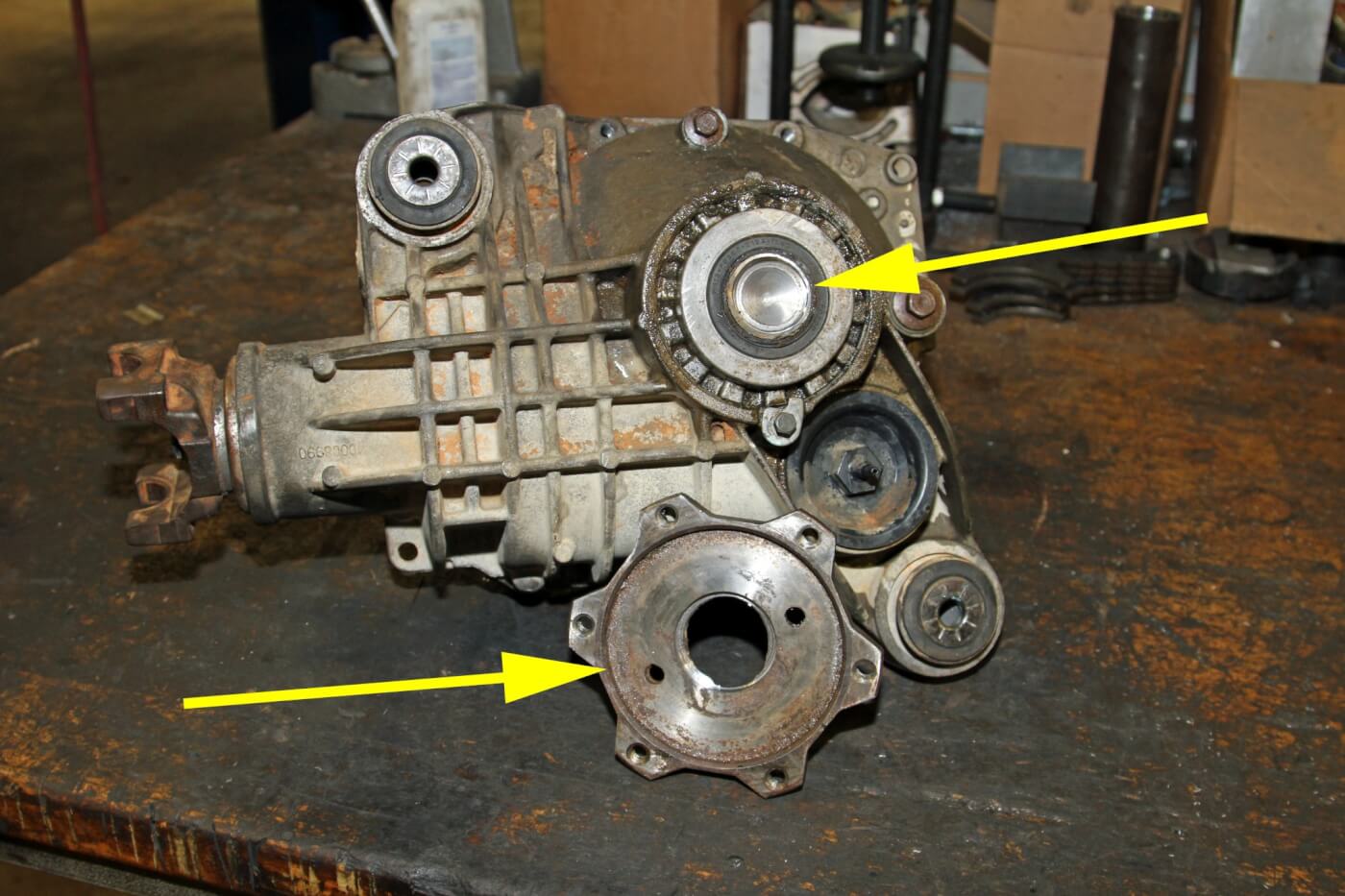
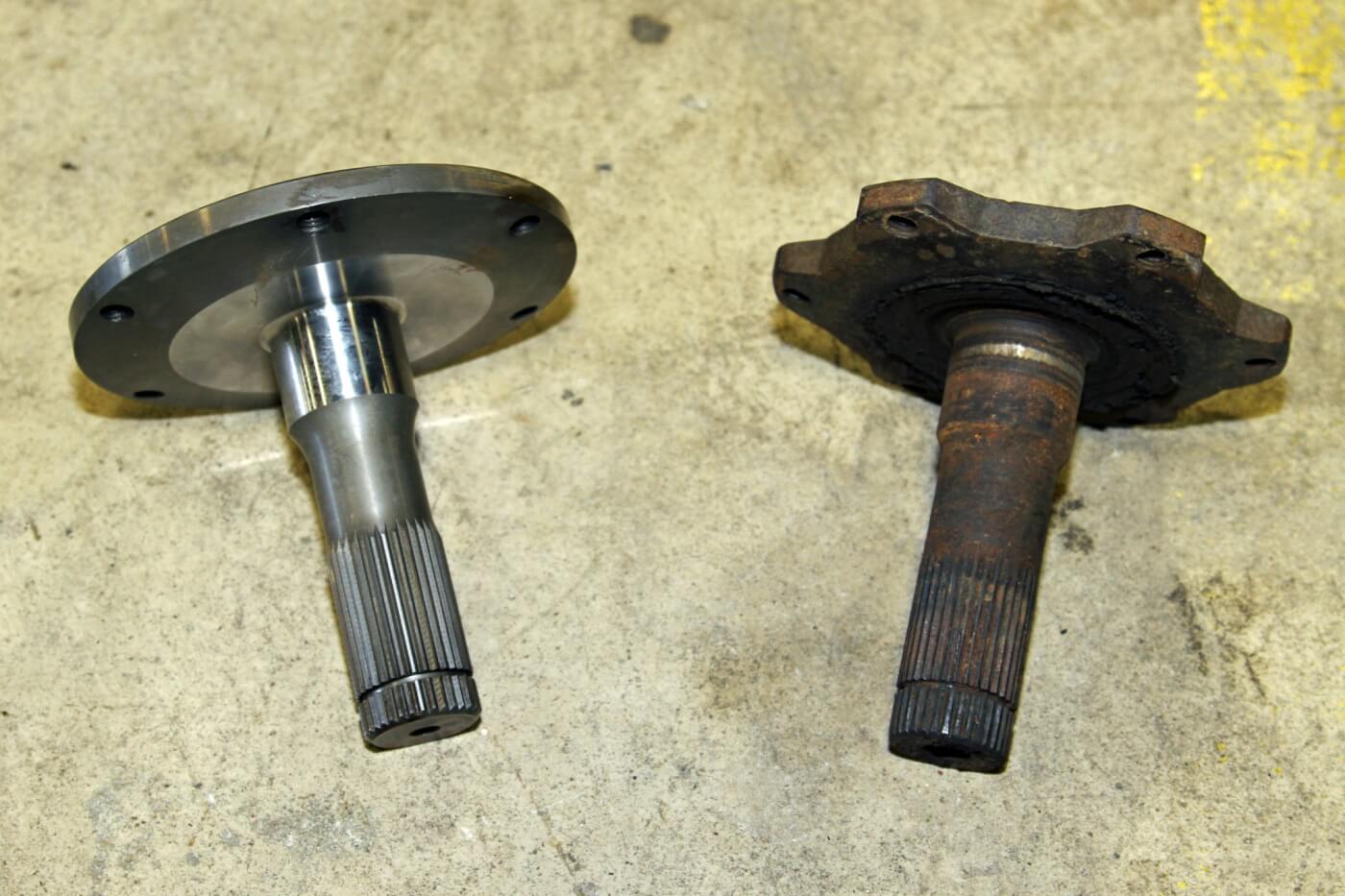
The RCV axle assemblies use their unique Chromoly Super Duty Dome-Mass Cage and Race at the steering end of the axle. This part is capable of handling 45 degrees of articulation with greater strength than factory CV joints. Chromoly axle shafts link the outer joints to the Pro4 Super Inboard CV joints on each side. The inner CV is protected with a rubber inner boot to keep the grease in the joint, and a rugged nylon woven over-boot to protect the inner boot from trail hazards. The outer joint uses RCV’s patented orange SST cast polyurethane dome seal to protect and seal the joint. RCV also makes their Ultimate CV axle shafts for the AAM 9.25 straight axle for Dodge Ram owners who want more strength and capability.
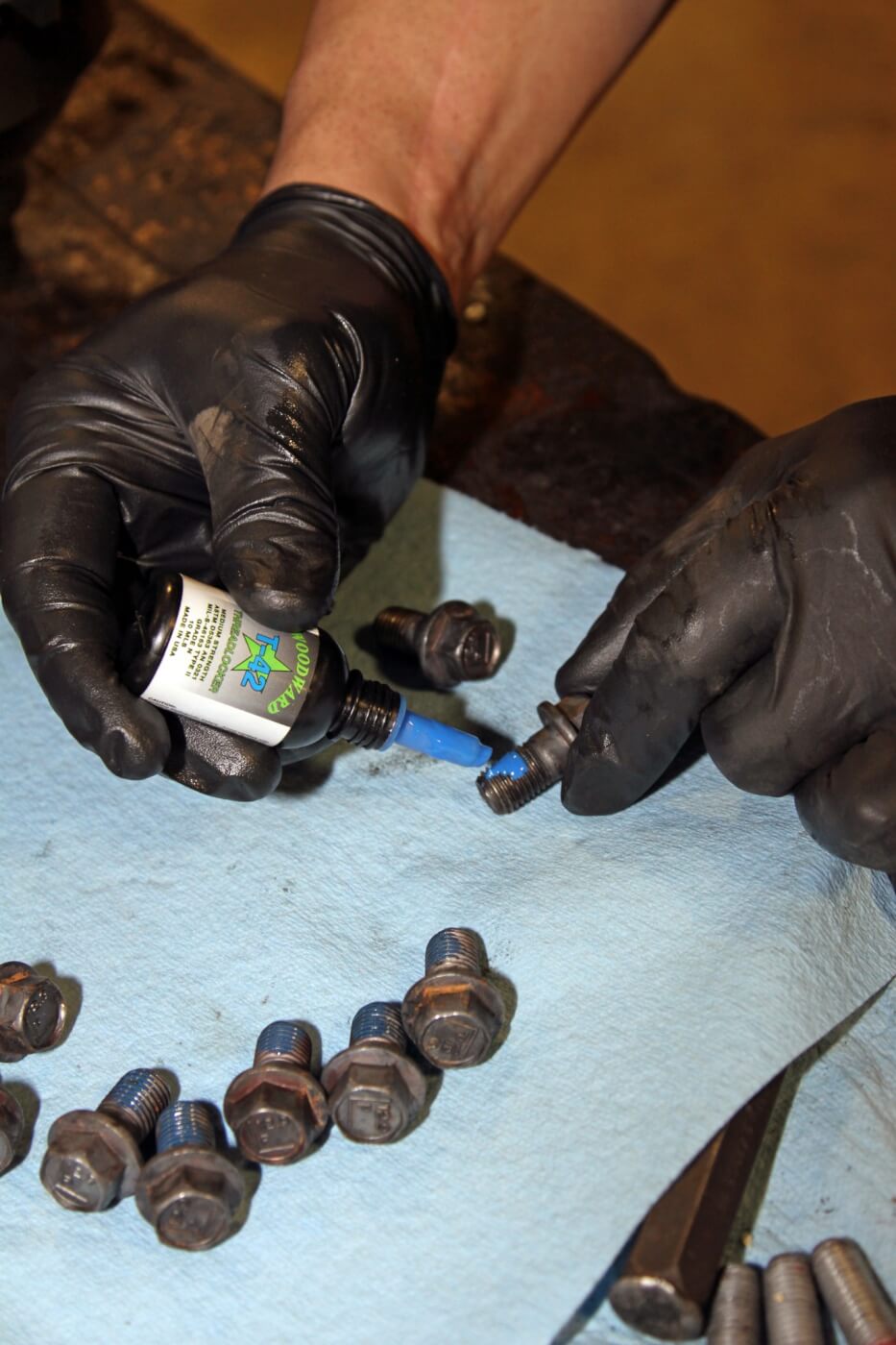
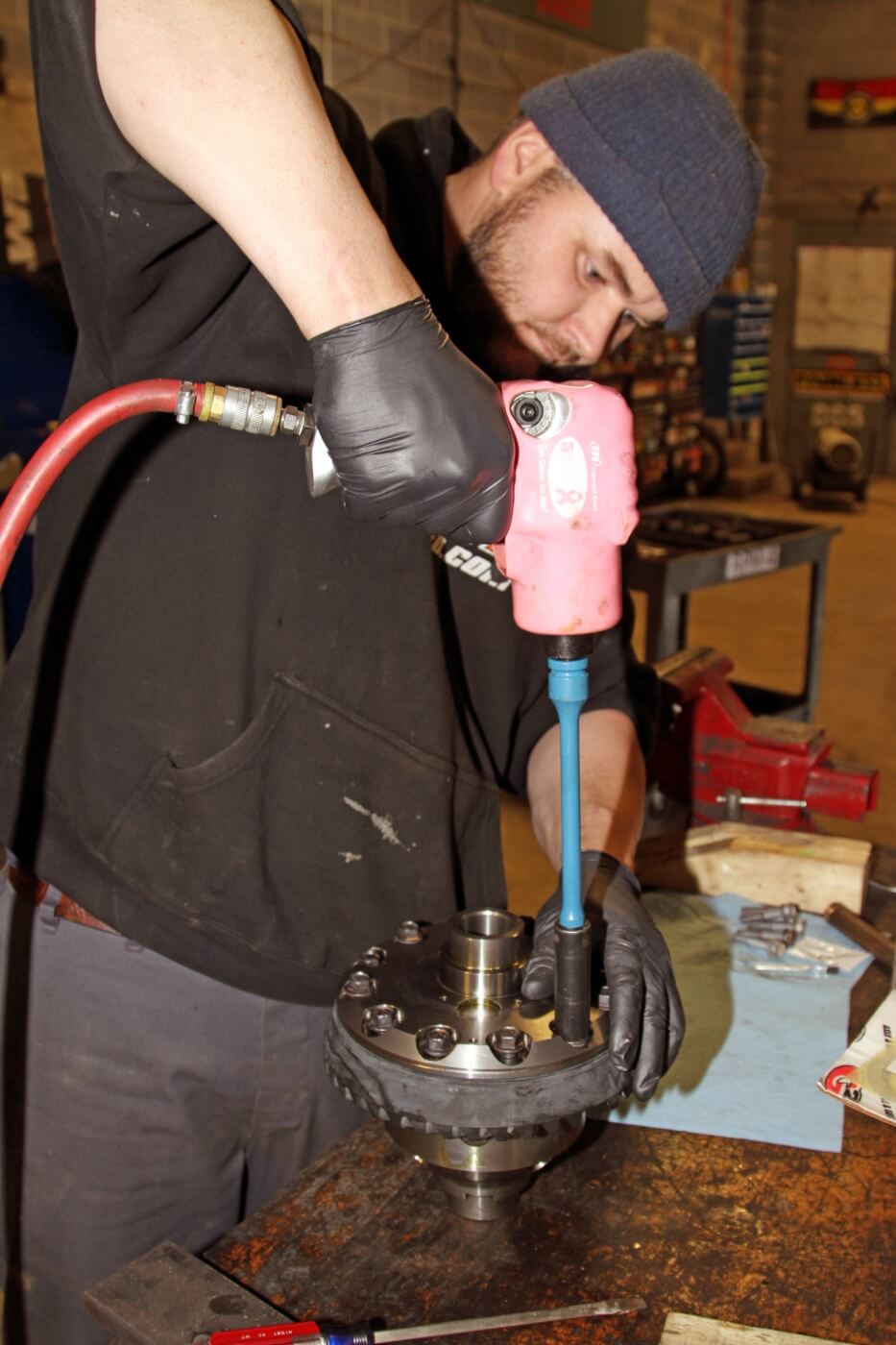
PERFORMING THE INSTALLATION
As with the rear axle, RPM Offroad installation technician Jason Nelson led the installation team in removing the CV axles and differential from the truck. Unfortunately, after the differential was removed, Jason realized that the driver-side axle shaft retaining clip was seized in the axle. The housing had to be sent over to Twin City Auto Machine to have the flange milled off the shaft so that the housing could be split to open the aluminum differential case. While this isn’t necessarily a common problem, it does happen from time to time and if it happens to your truck, you will need to replace the driver-side shaft. In our case we were replacing both shafts so it was only a time delay while the machining was done.
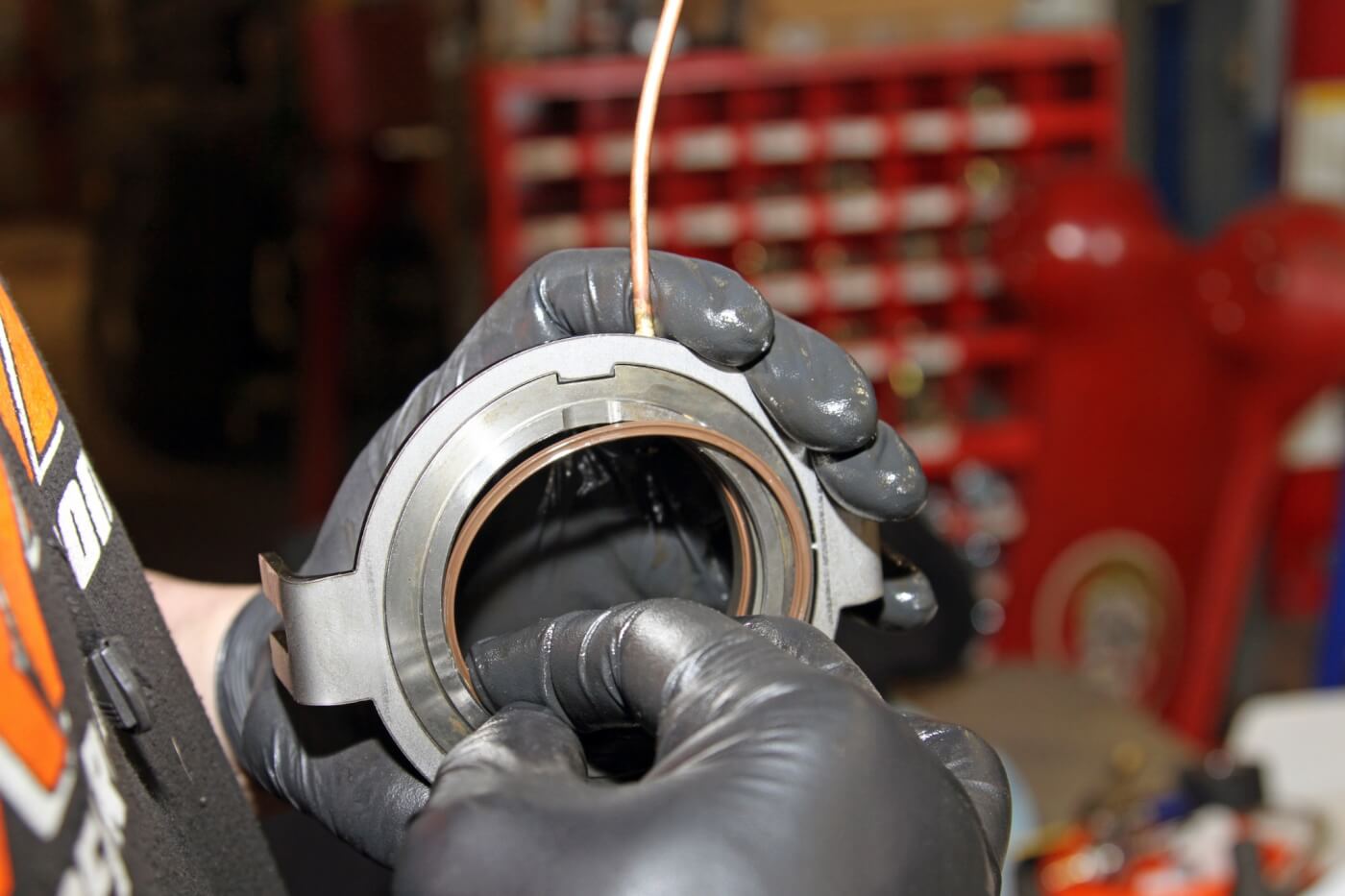
The ARB locker requires a high-pressure air supply for activation. ARB offers several compressor options ranging from small ones designed to operate just the locking differentials to large ones capable of running air tools. We opted for the large ARB Twin compressor along with a 1-gallon aluminum tank and accessory kit. This would allow us to have air to inflate tires and run tools to work on the truck in the field. Nelson installed the compressor, tank and manifold on an aluminum panel secured to the floor of the bed on the passenger side, a placement that provides easy access to the air hose connection.
After the installation was completed, Nelson filled the differential with Royal Purple 75W-90 Max Gear synthetic gear oil. Many owners choose to use cheaper gear oil for break in since it will be changed soon, but we chose to use the good stuff from the get-go.
TECH TIP: Don’t forget to drain the oil and refill the axle after a 500-mile break-in period.
Installing the RCV Ultimate IFS CV axles is as easy as removing the factory CV axle assemblies and replacing them with the RCV units. You will need a band clamp tool to install the over-boot; RCV sells two models to do the job.
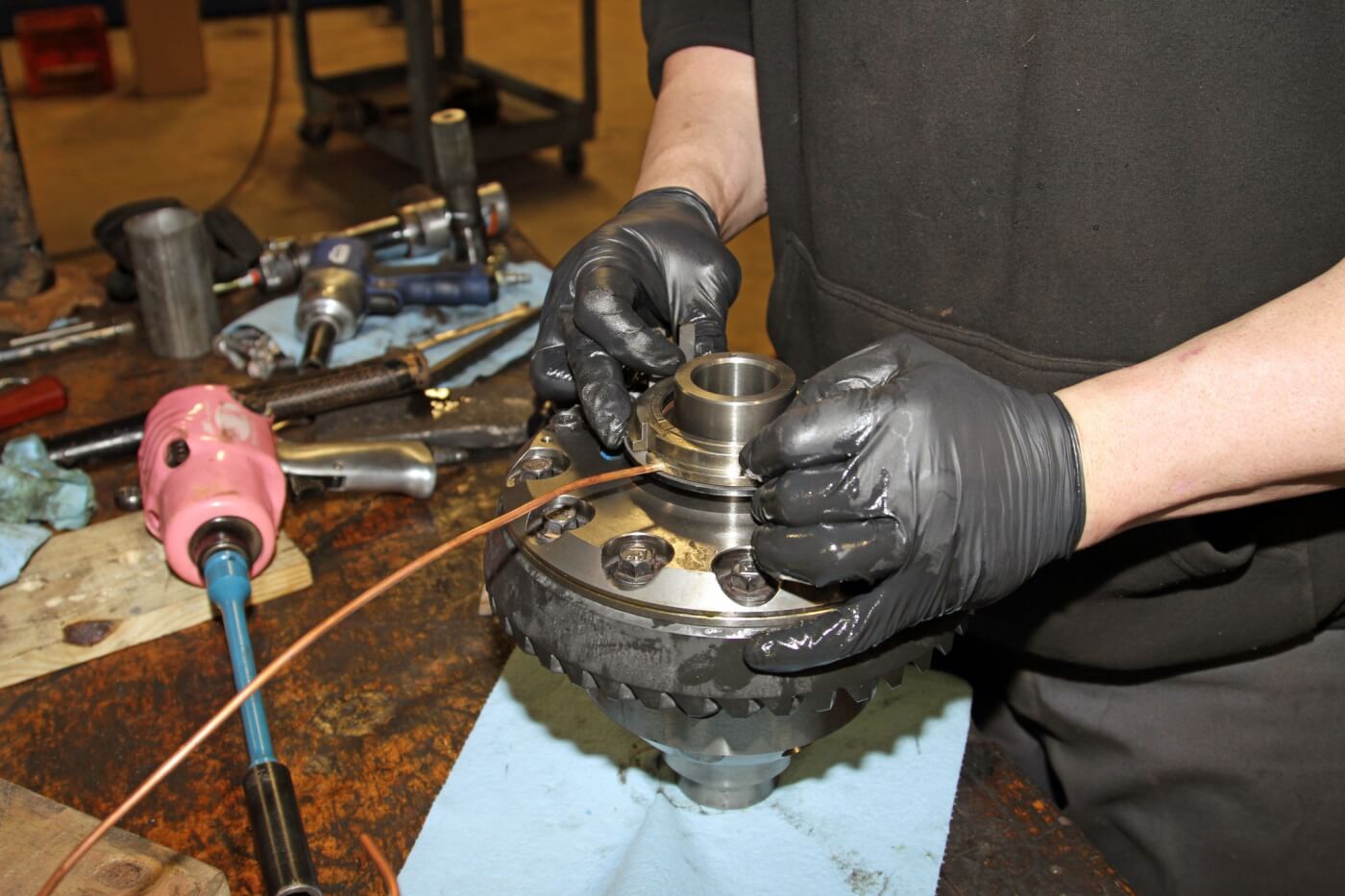
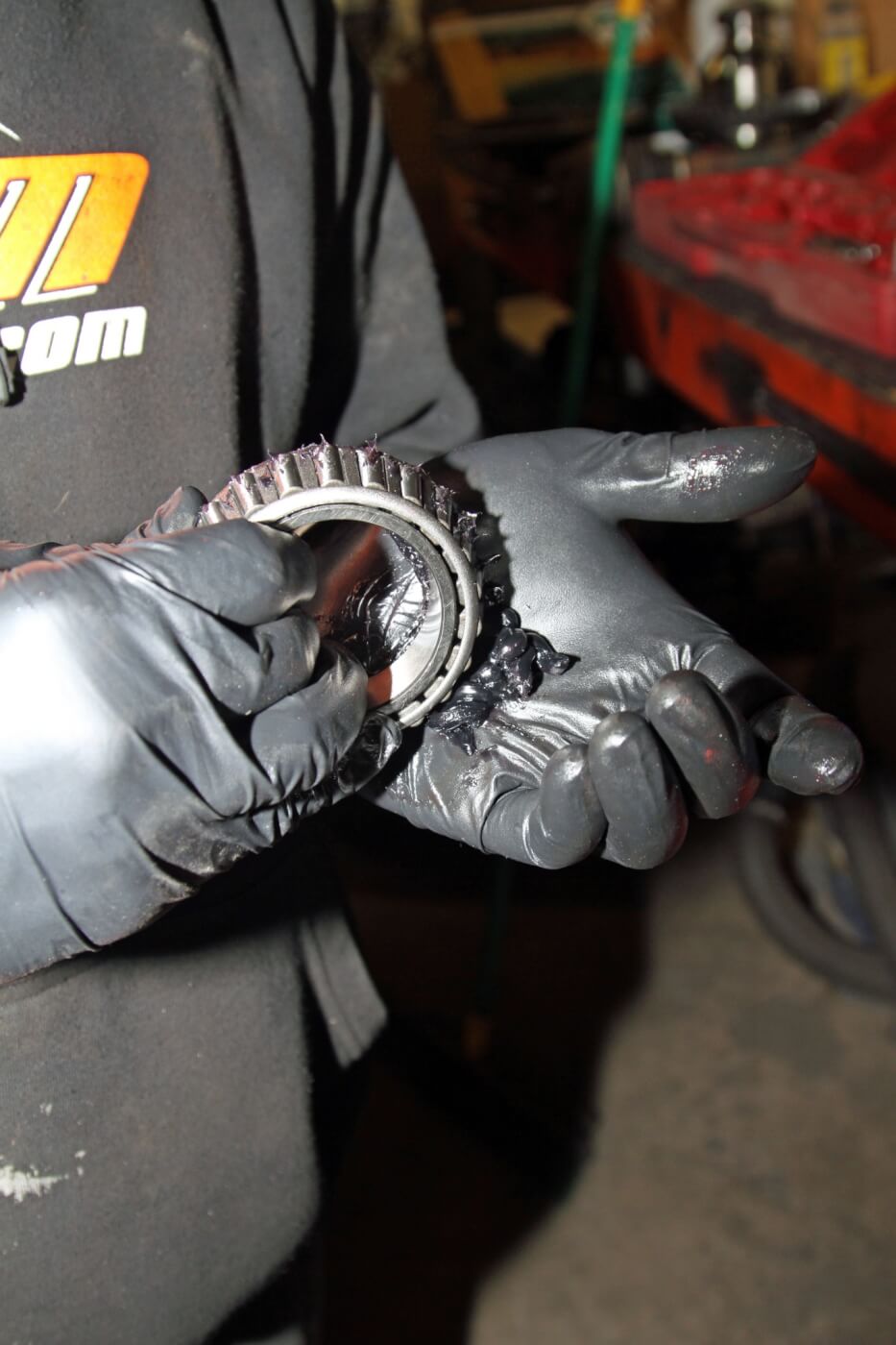
Installation of the Fleece Performance TufShafts is also pretty straightforward (provided you don’t have seized retaining rings as we did) and can be handled by an average DIYer. Installing the ARB Air Locker and setting up the new G2 gears does require more skill, however, and we recommend having your local diesel performance or off-road shop handle it for you. ARB provides great instructions for those who have the knowledge and skills to set up the gears and install the locker, but improper setup could lead to premature wear in the gears that would not be covered under warranty.
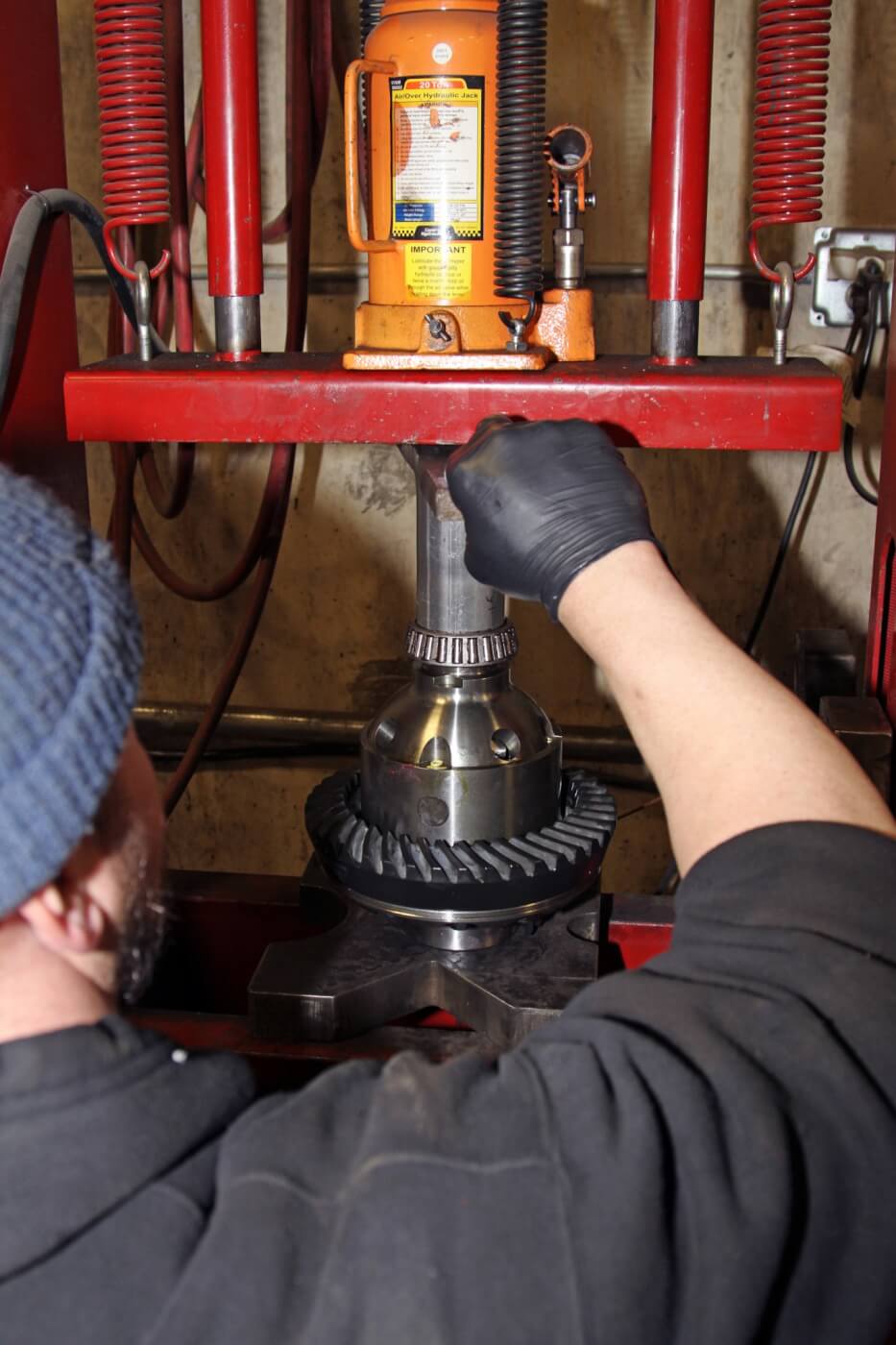
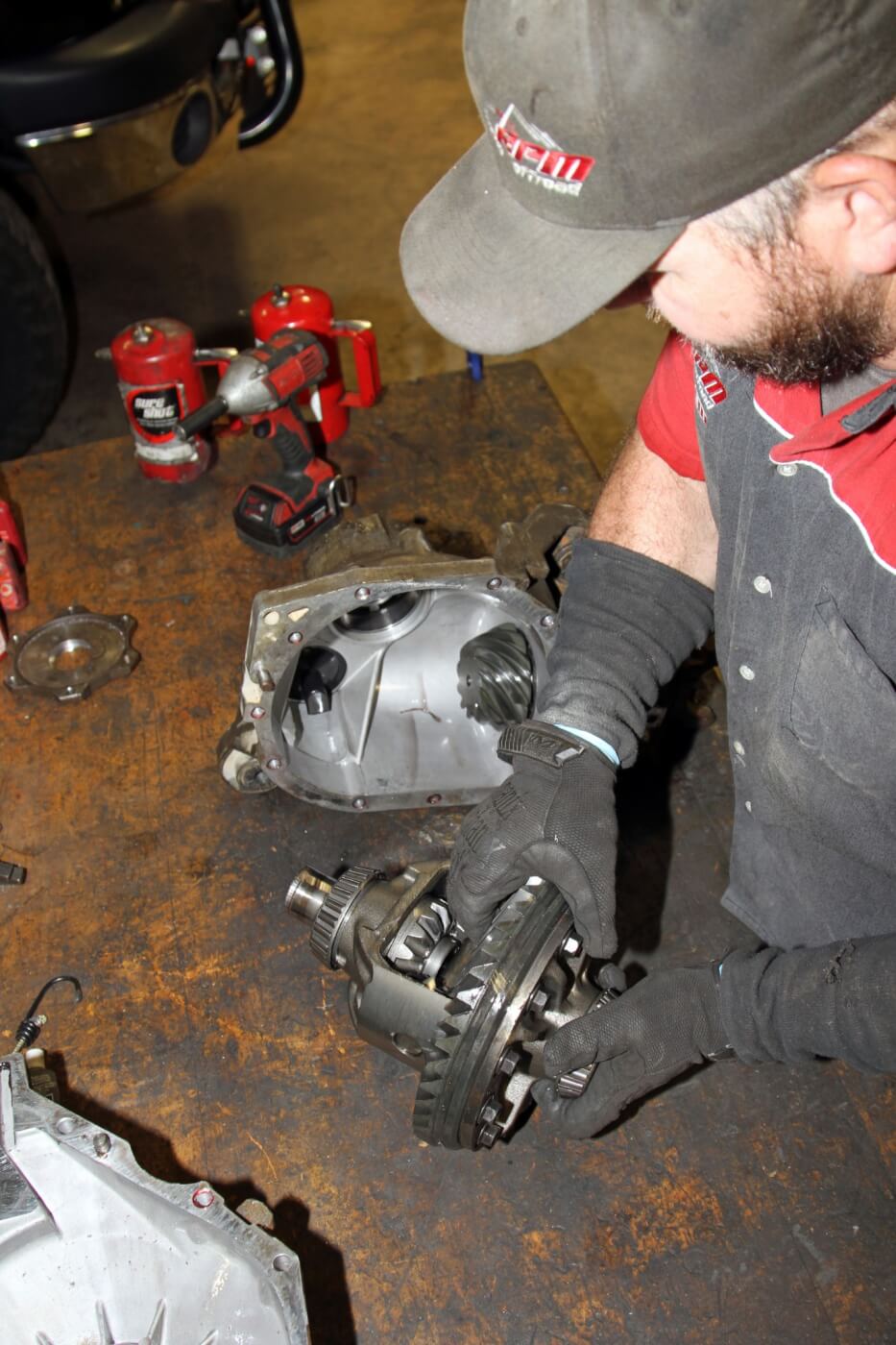
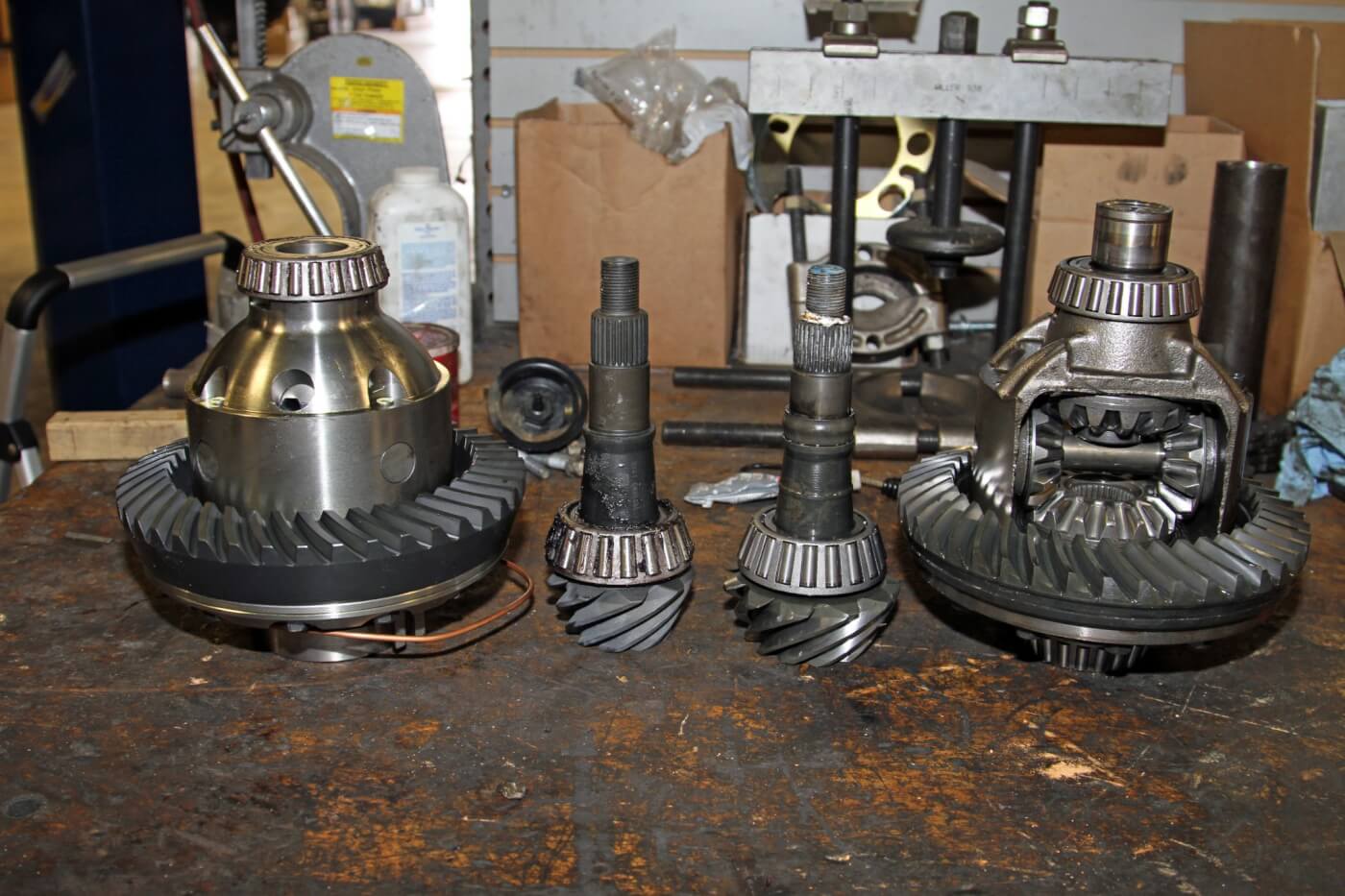
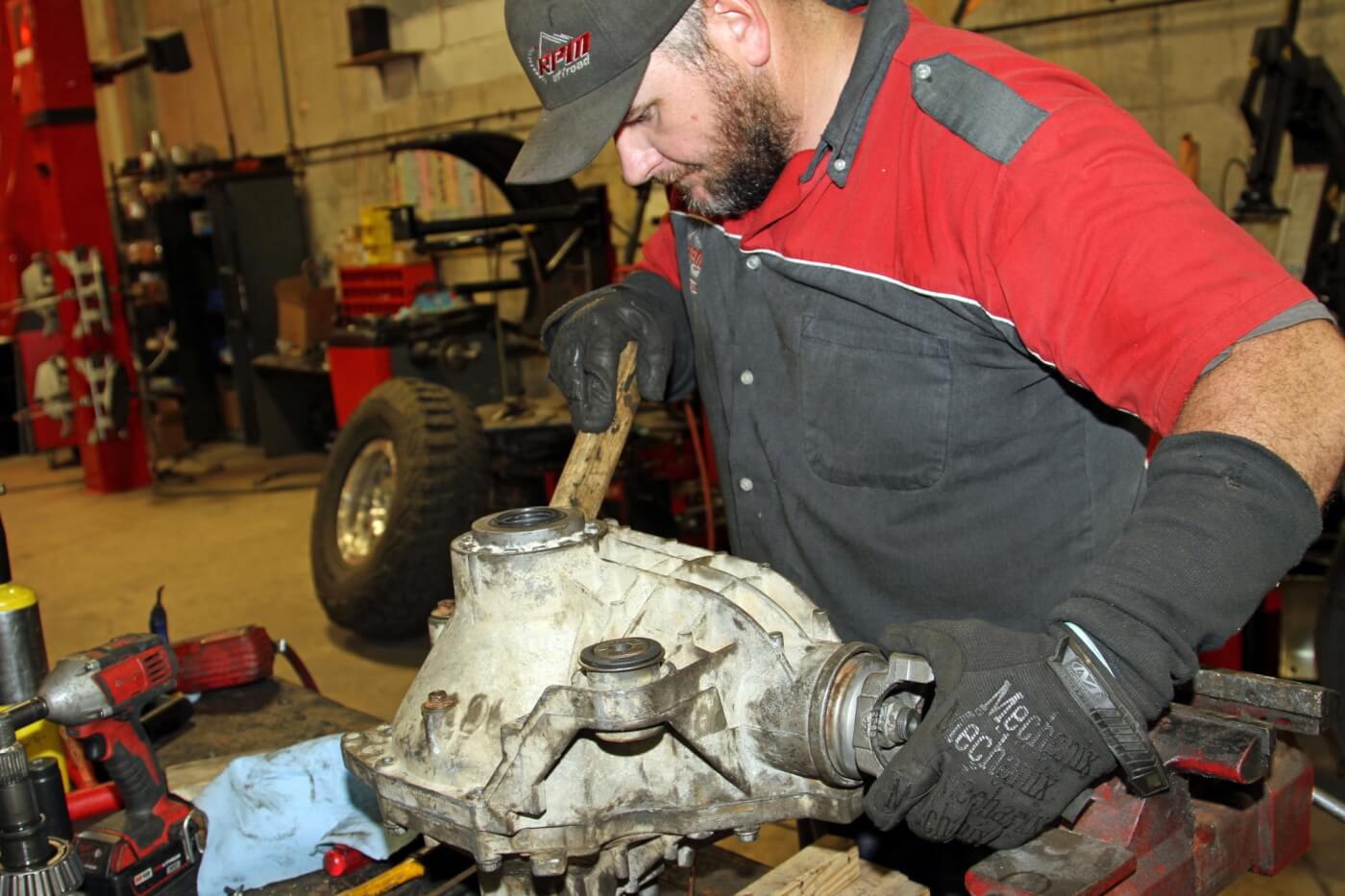
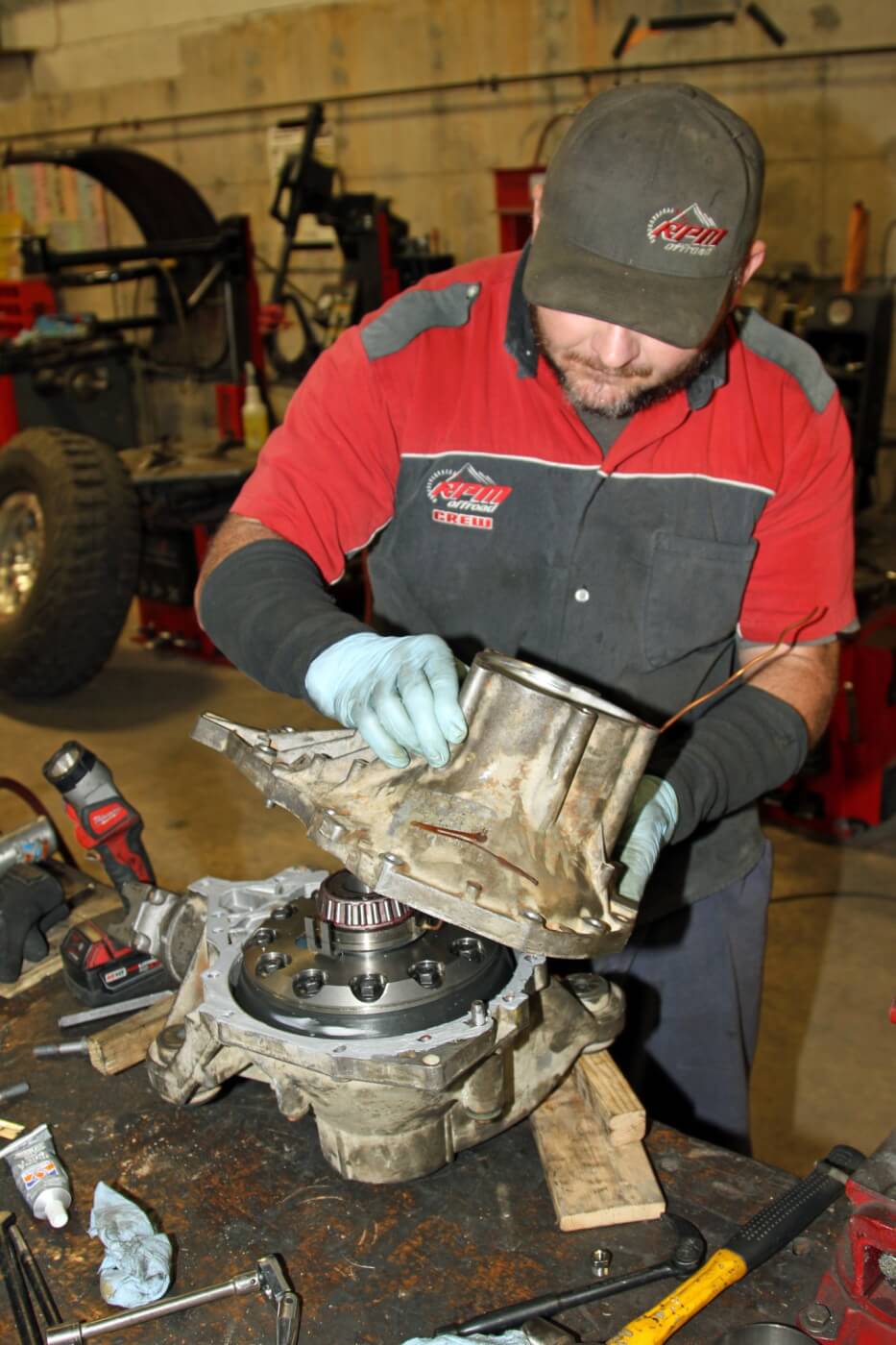
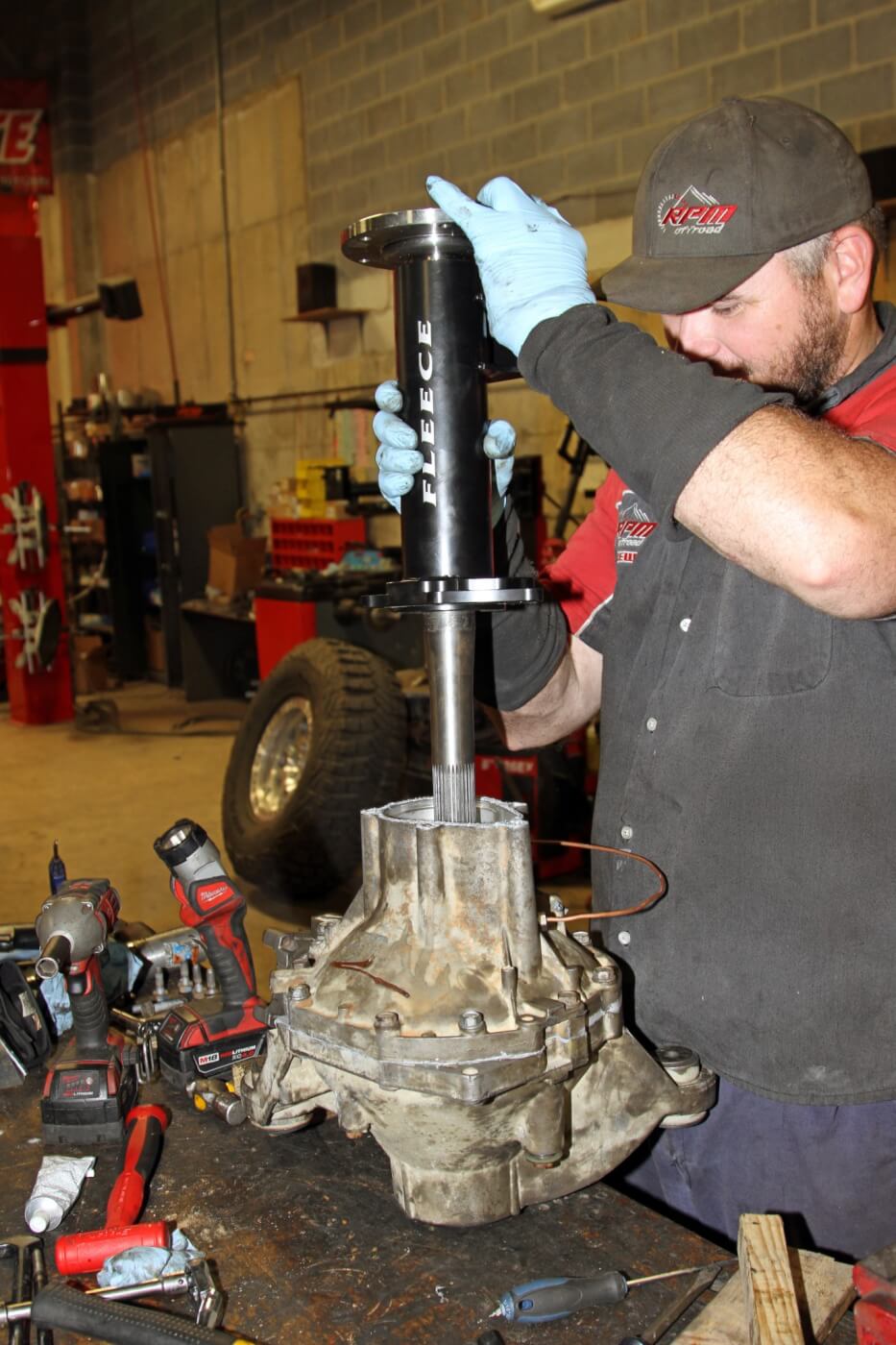
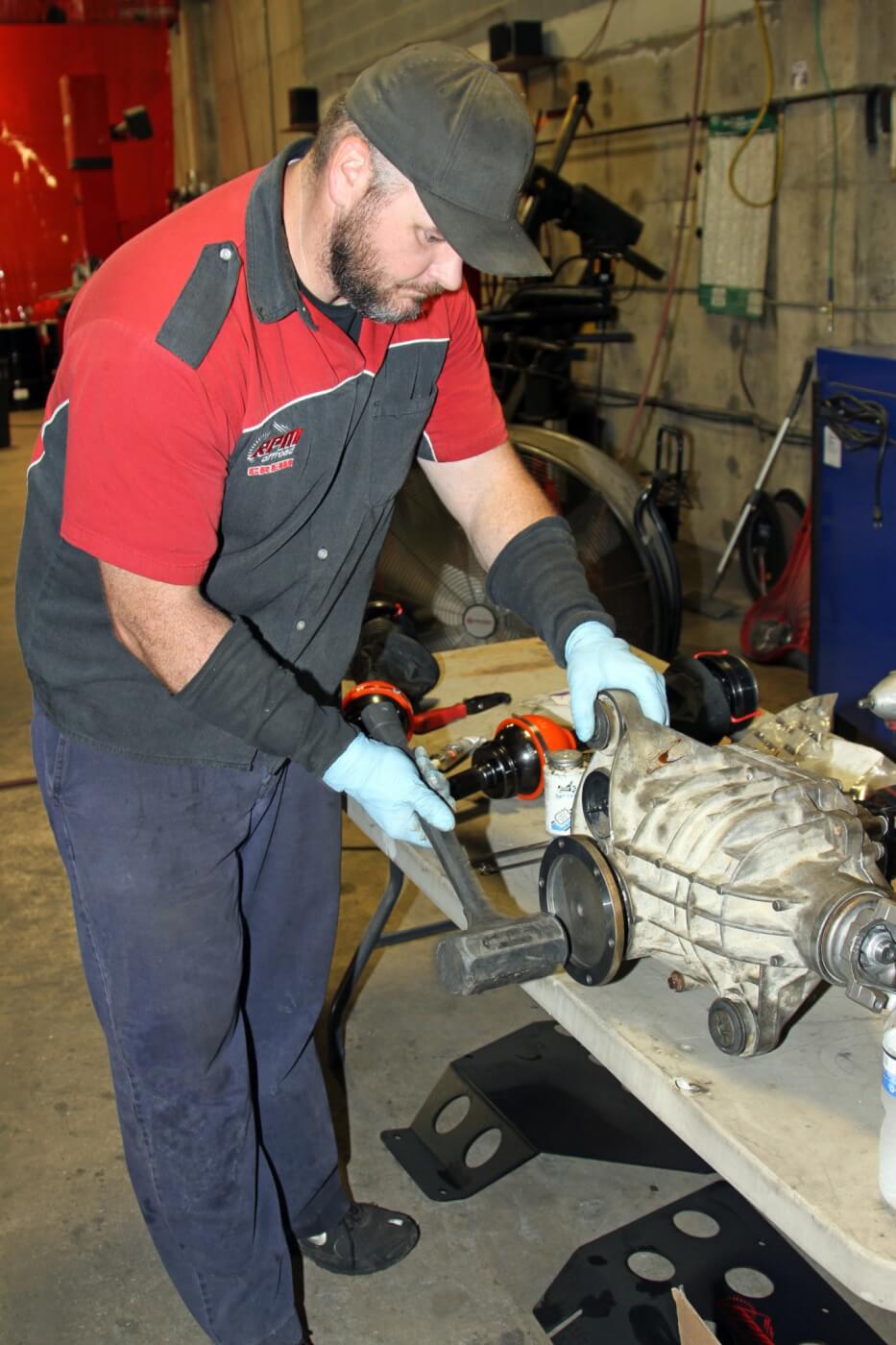
GREAT RESULTS
After the project was finished we had the opportunity to put the truck through its paces at the Adventure Off Road Park in South Pitsburg, Tennessee. We were already onsite to cover an off-road race. With great traction at all four corners of the truck we were easily able to traverse steep, muddy and rocky trails through the Tennessee wilderness and get the large truck in and out of areas that others thought would be impassable. We have also run the truck in the dirt drags at Bean’s Diesel Performance and we were very happy with the results. If you want more strength and traction out of your IFS GM truck or AAM 9.25-equipped Dodge Ram, upgrading your front axle assembly is a great way to do it. DW
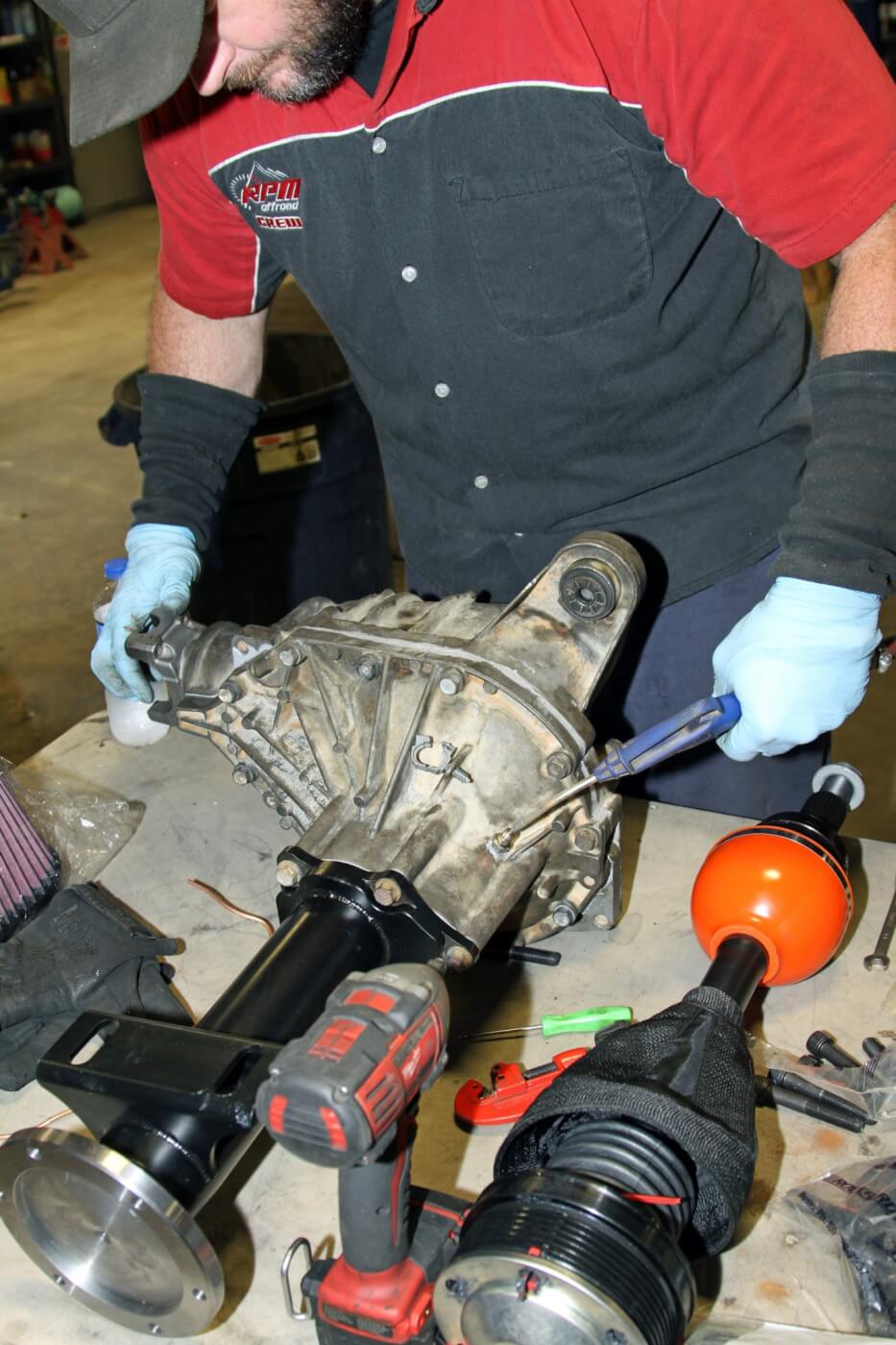
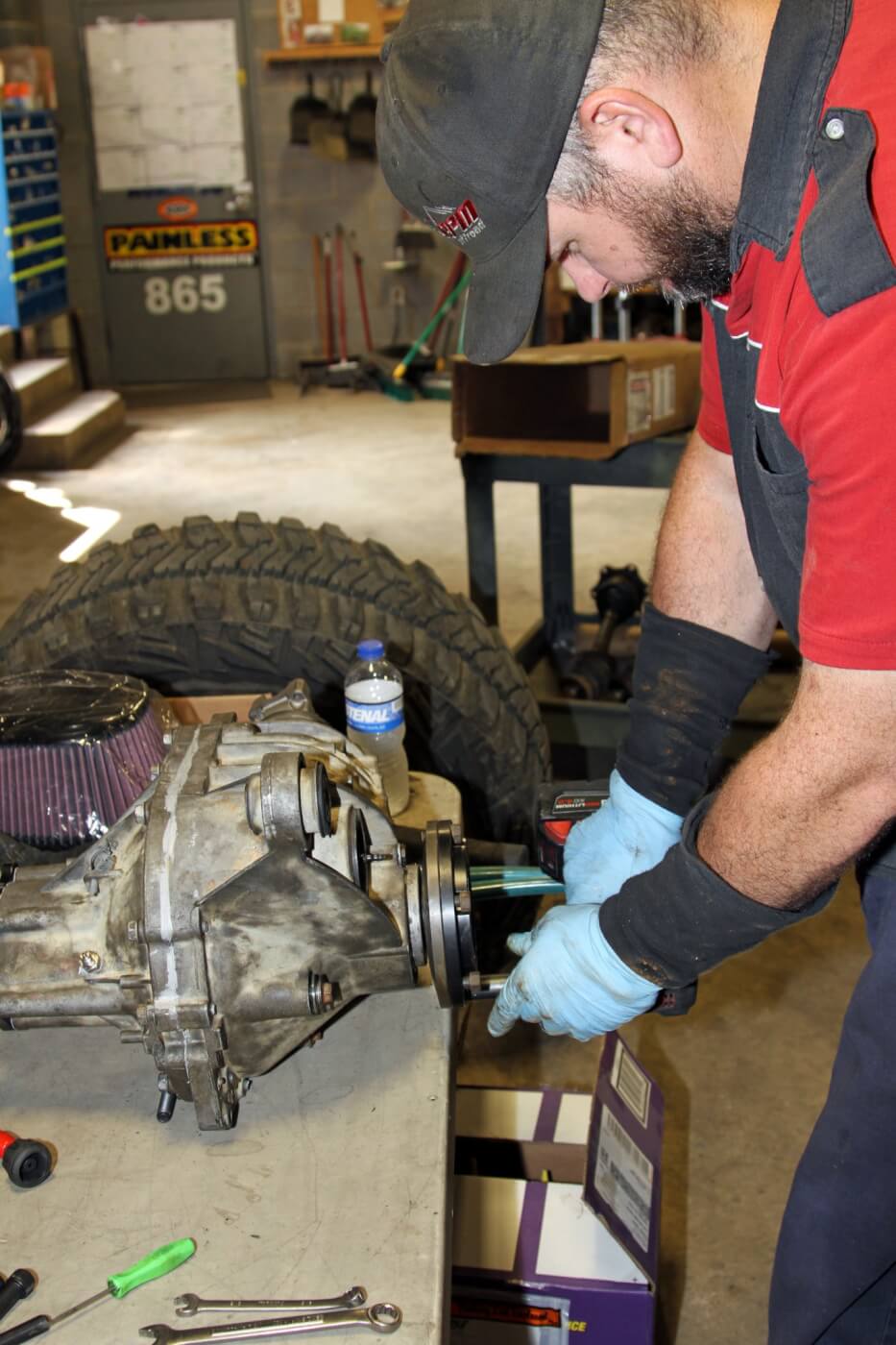
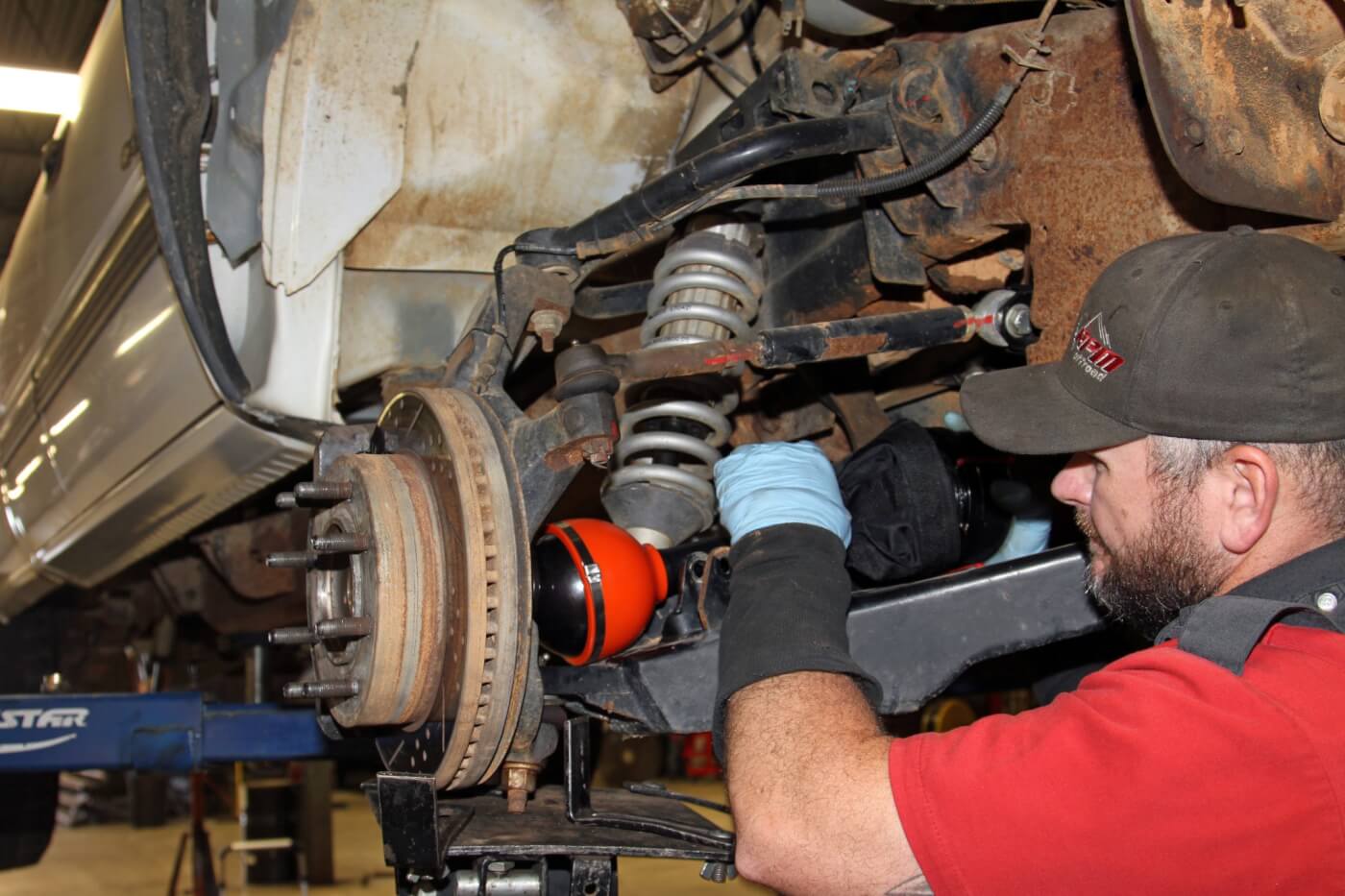
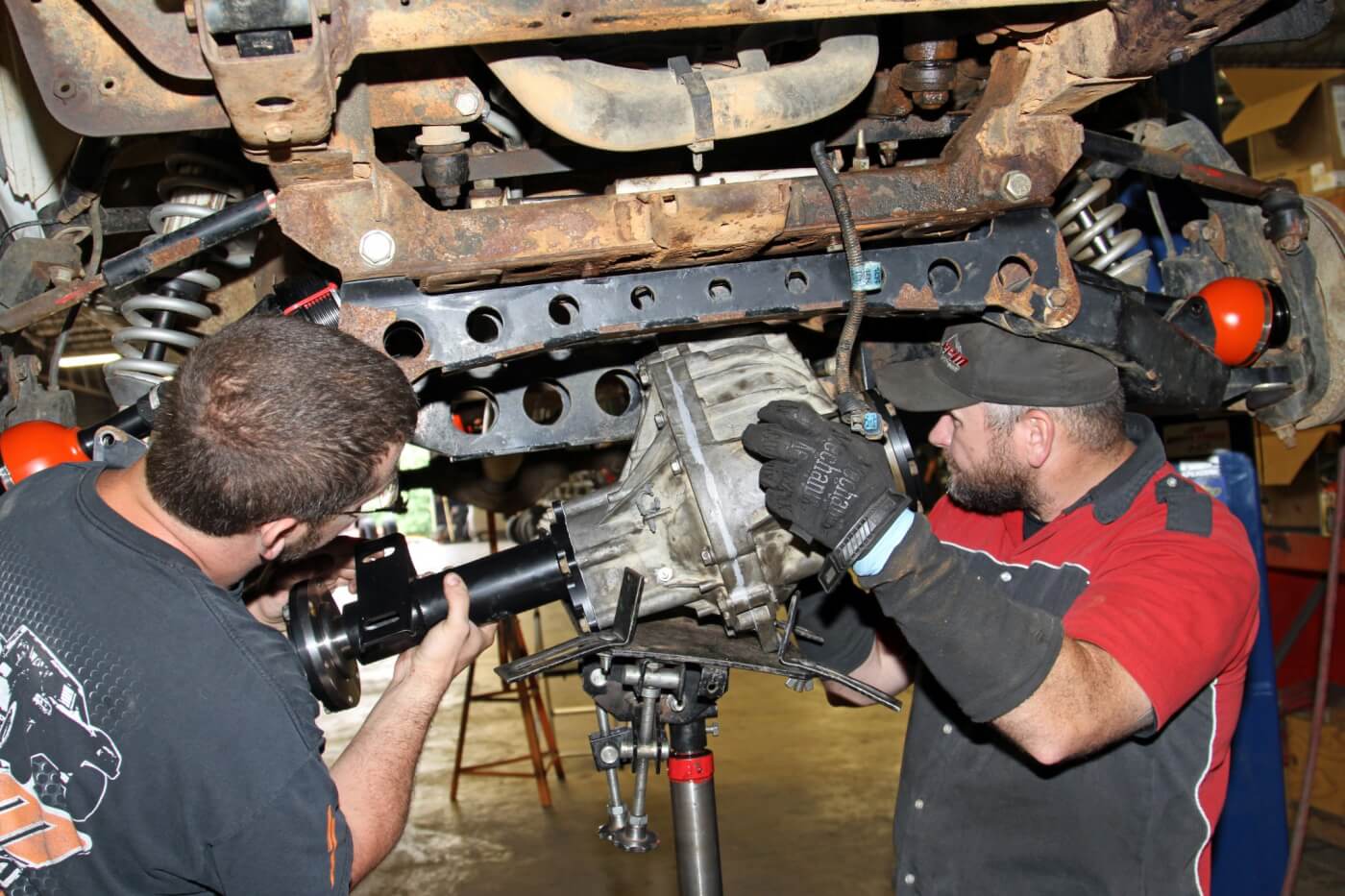
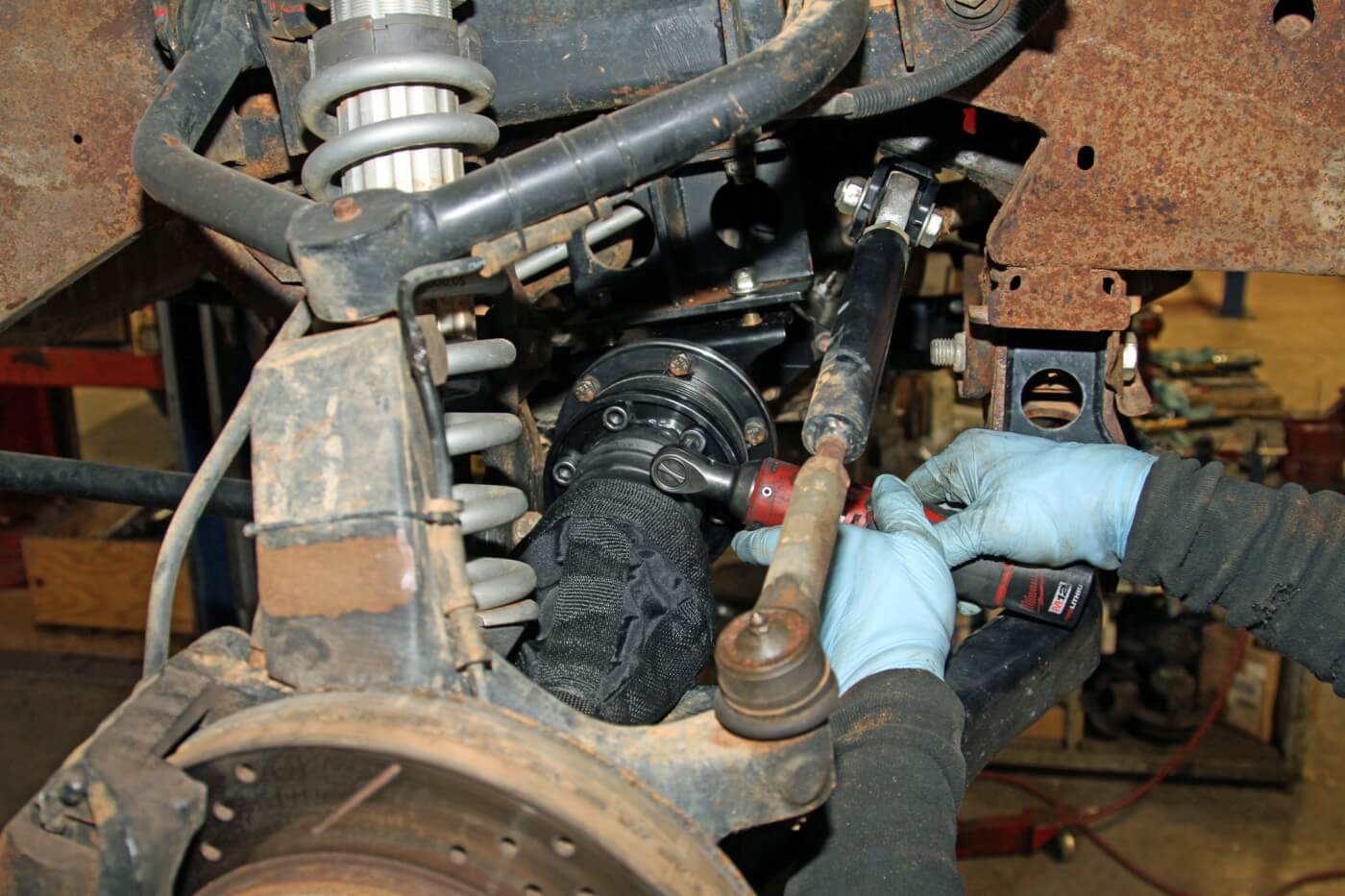
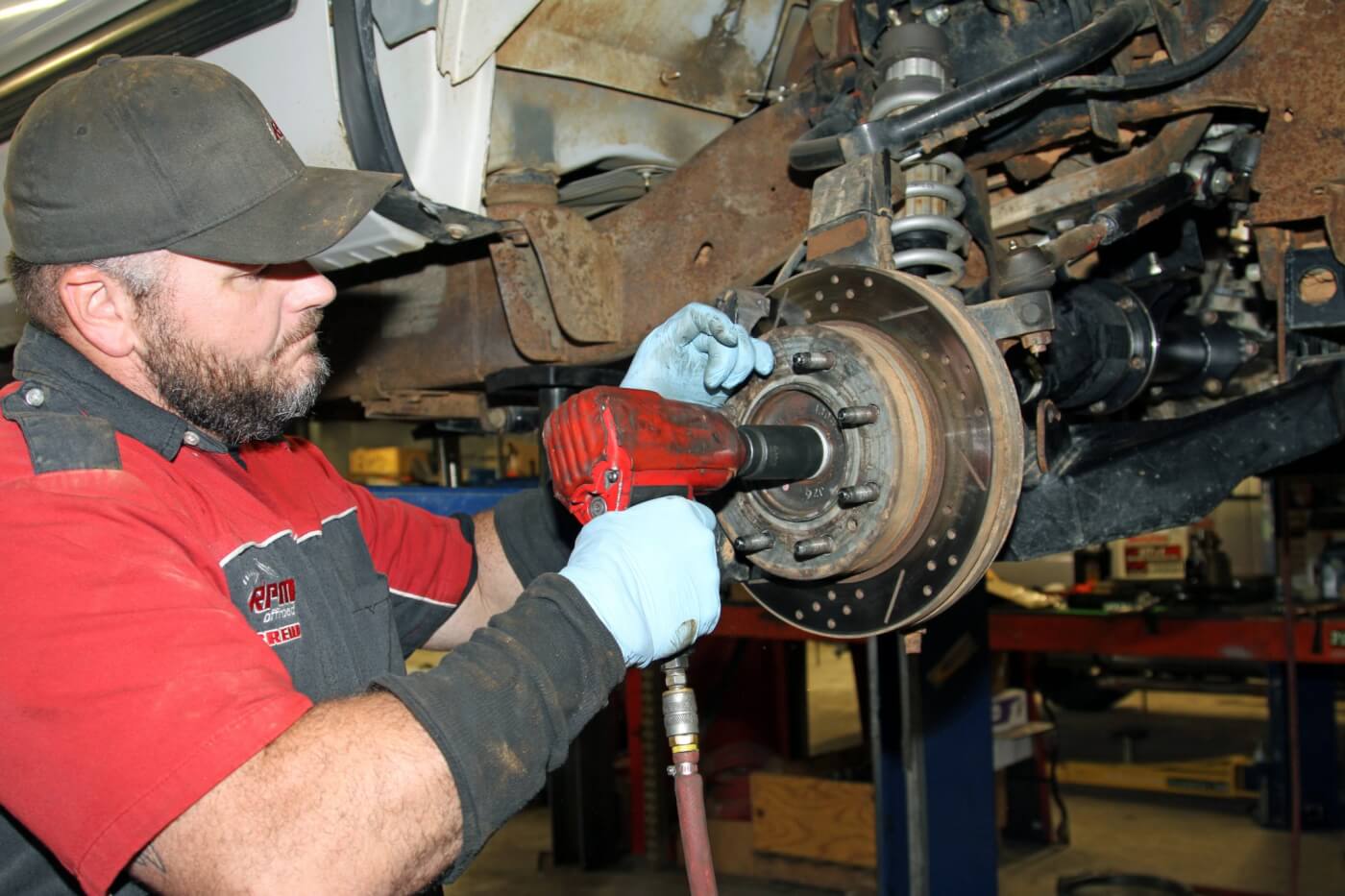
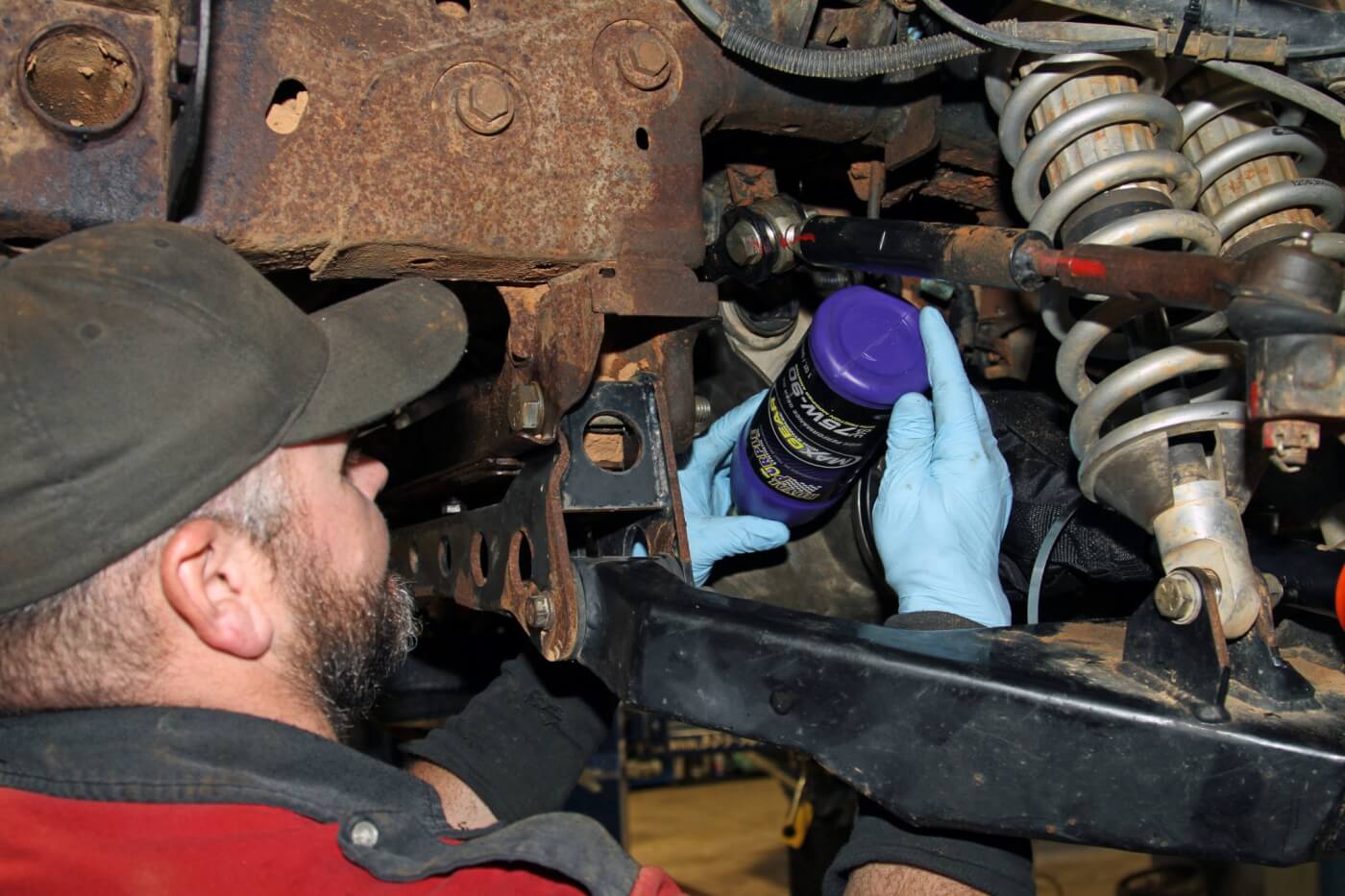
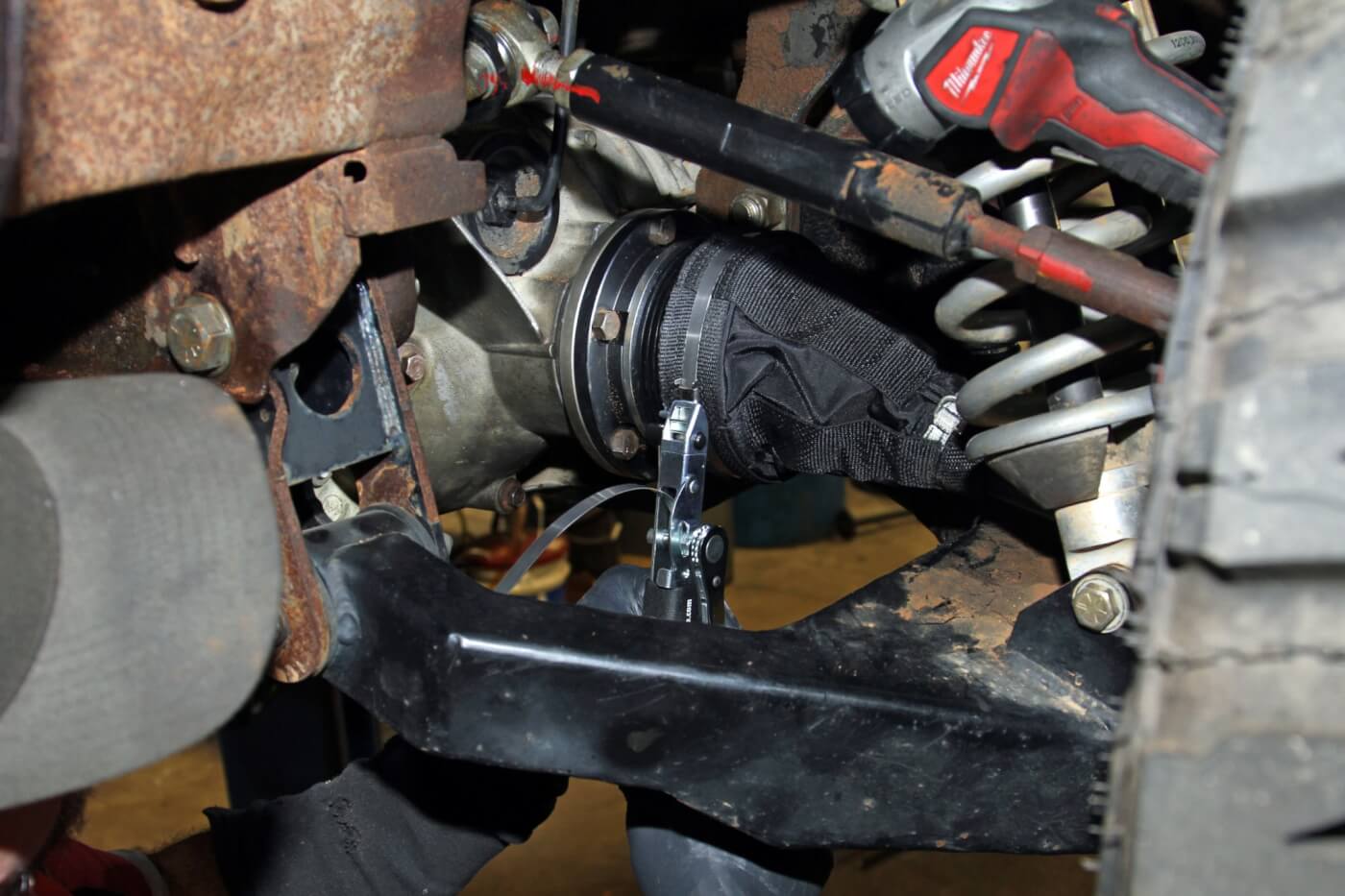
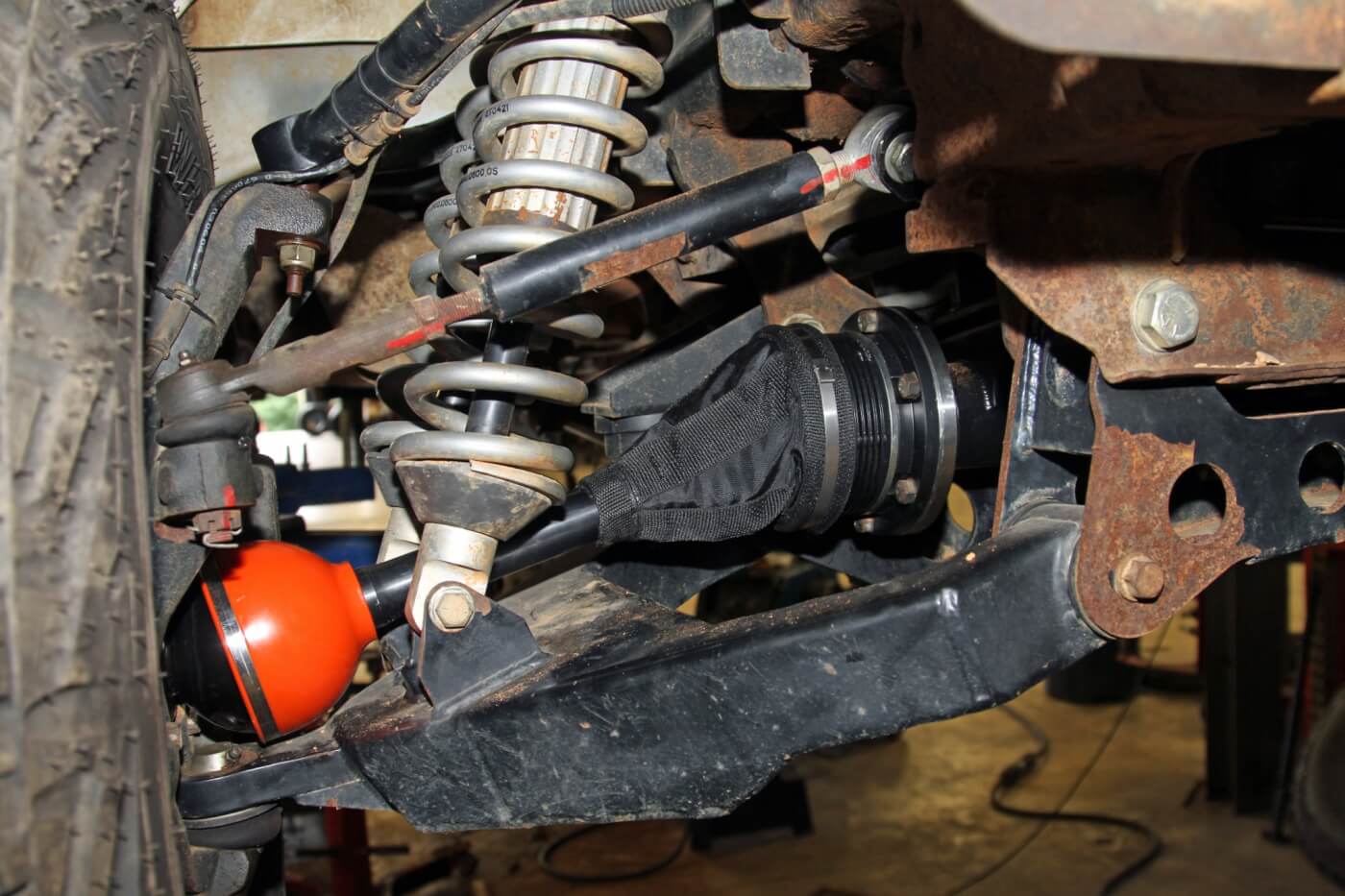
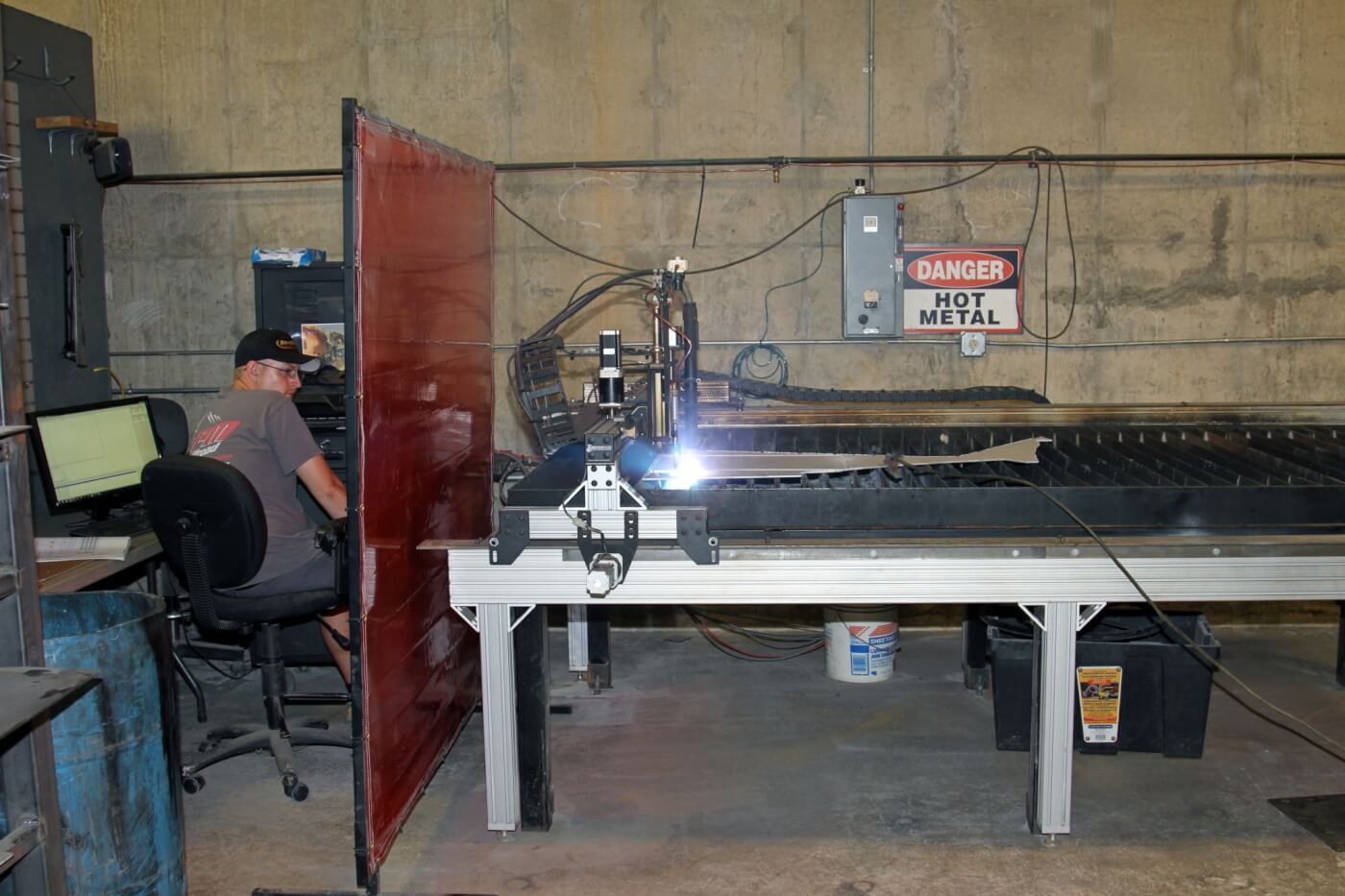
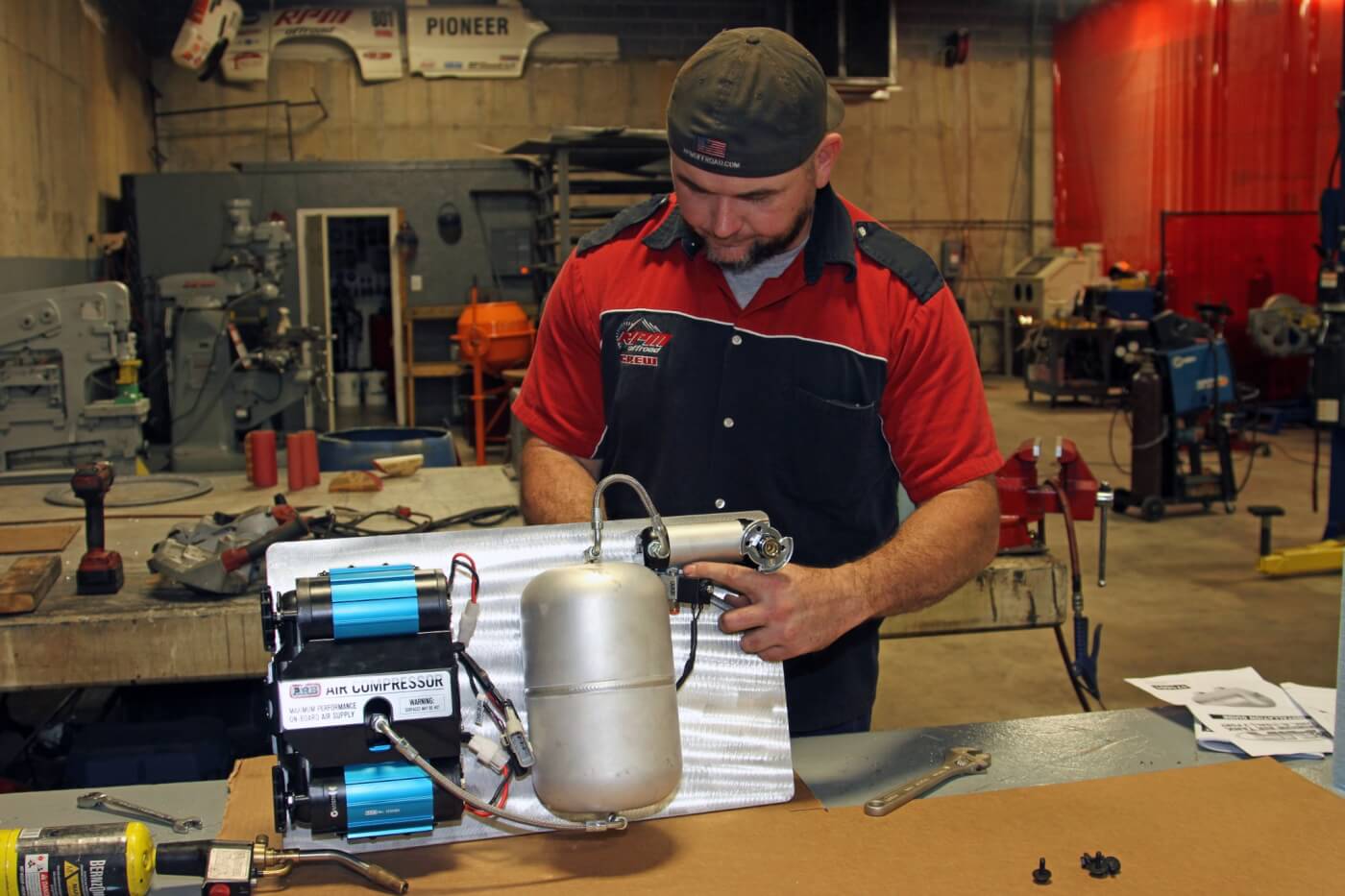
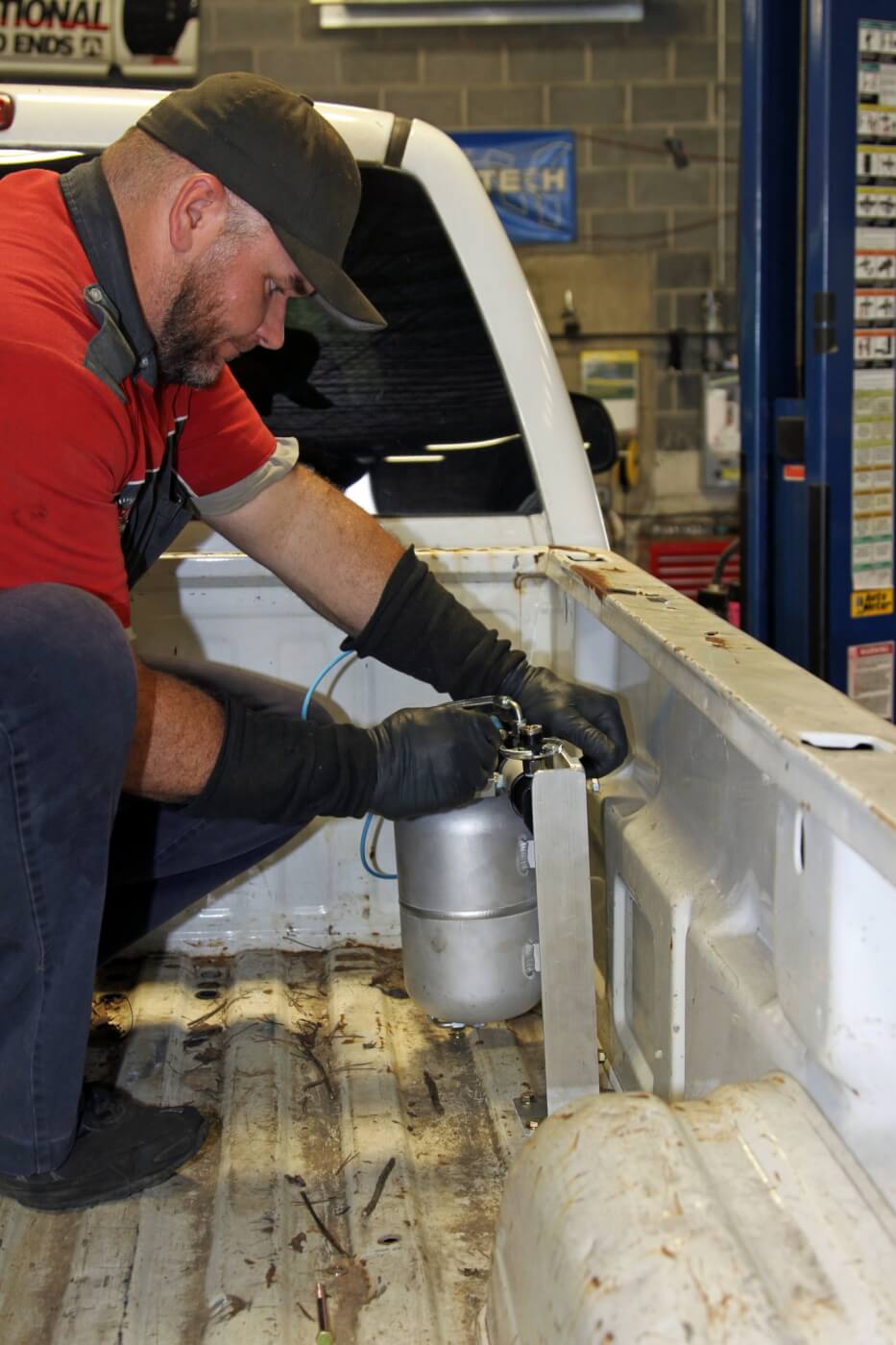
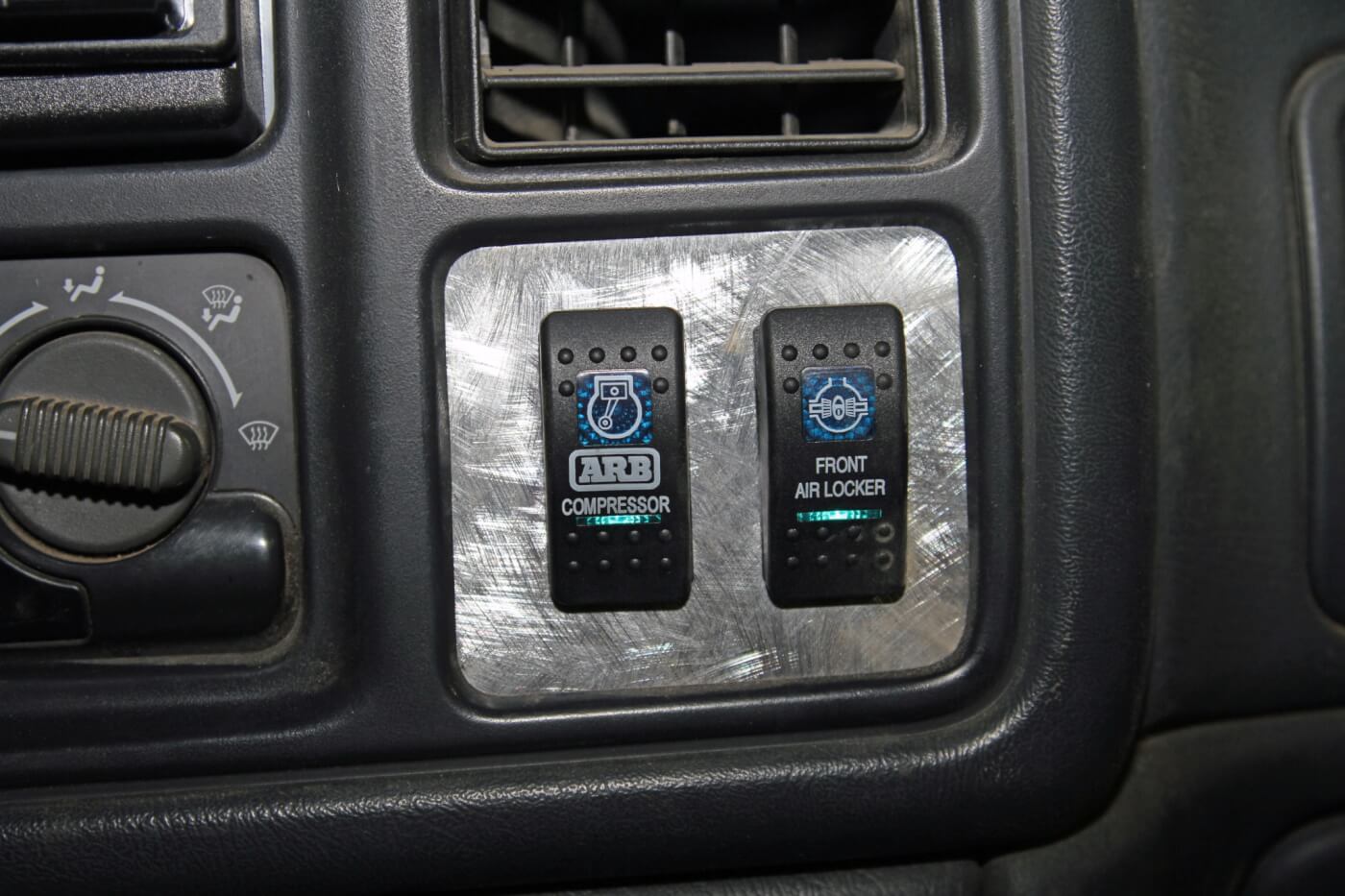
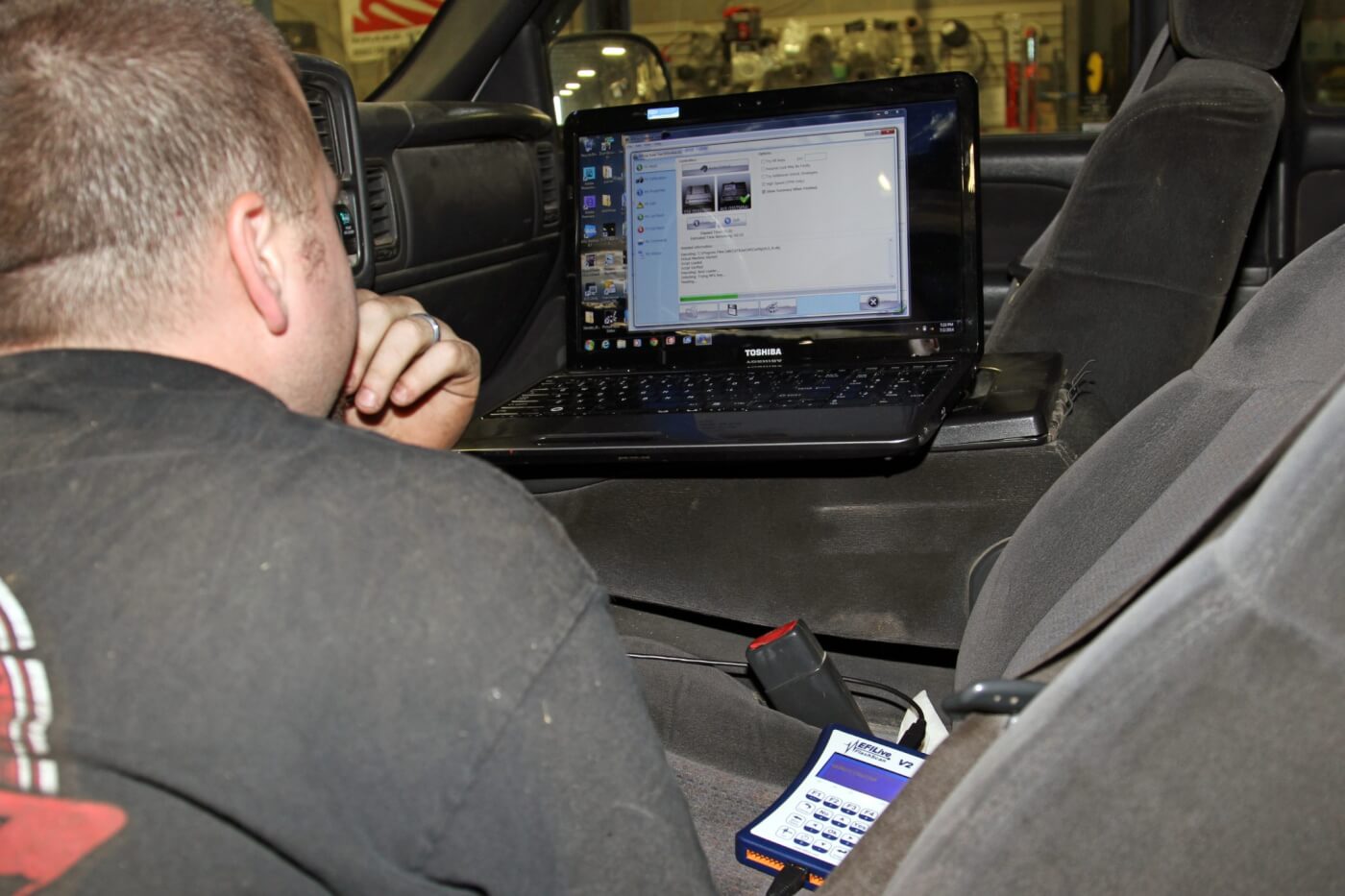
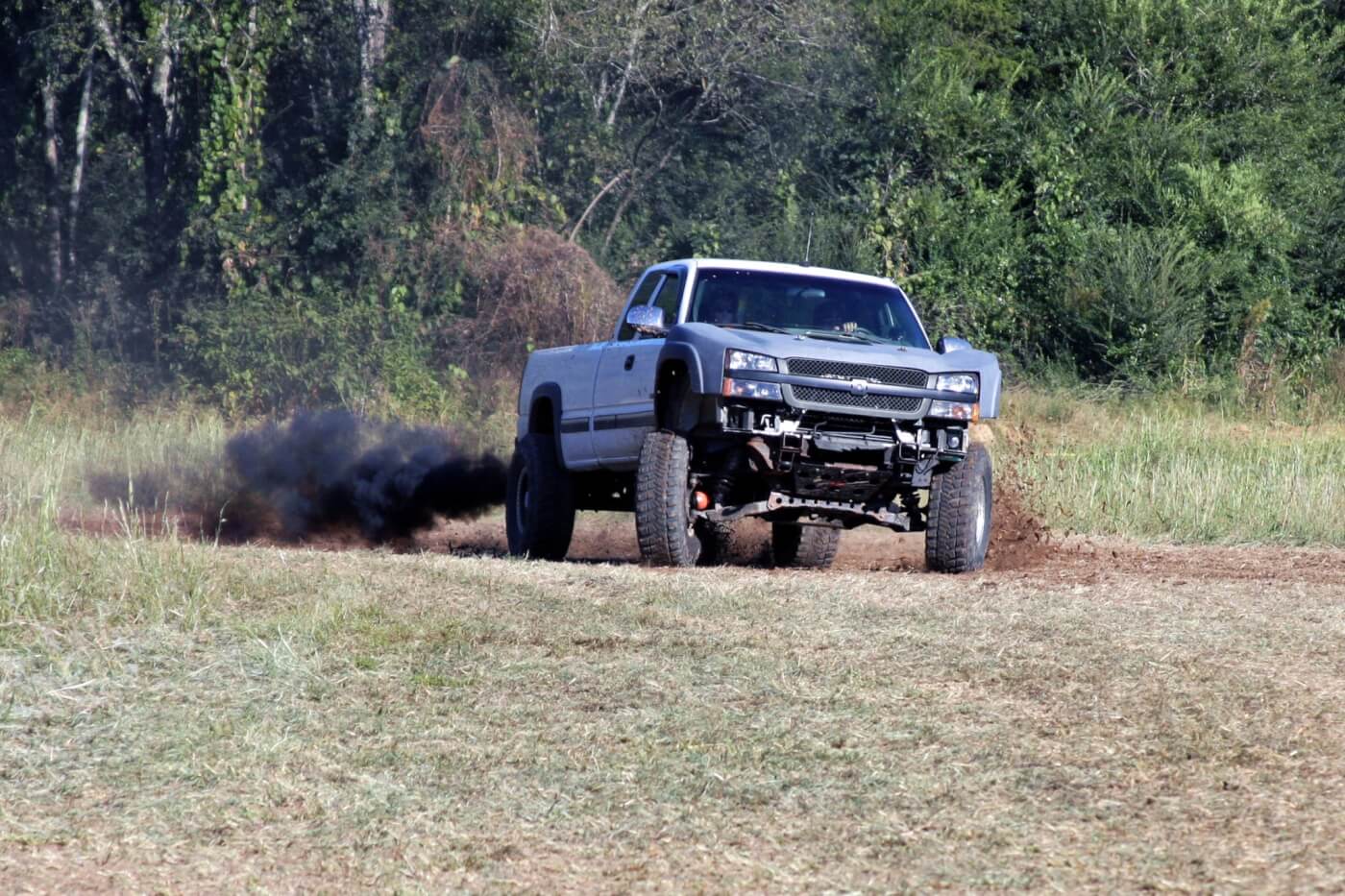
SOURCES:
ARB 4×4 Accessories
866.293.9078
EFILive
Fleece Performance Engineering
855.839.5040
G2 Axle & Gear
310.900.2687
RCV Performance Products
815.877.7473
Royal Purple
888.382.6300
RPM Offroad
423.573.3300
SoCal Diesel
661.775.5620
Twin City Auto Machine
276.669.1301
Woodward Race Products/
WRP Threadlocker
909.627.8286